Listen to this article ![]() |
While there is significant consumer interest around 5G for improved mobile device performance, there is also a great need among industrial companies to implement the technology within their facilities. This is because the demand for innovation and digitalization of factories has never been greater. When it comes to improving material flow, which in turn reduces machine idle time and other disruptions, the use of autonomous mobile robots (AMRs) in conjunction with other computing and connectivity technologies is often the best solution.
Indeed, the increasing size of AMR fleets and the expanding use of Industry 4.0 and industrial internet of things (IIoT) technologies on the shop floor is driving the need to adopt industrial-grade 5G private wireless communications. This upgrade to a more capable communications technology is needed to handle the increased networking loads with reliable, low-latency connectivity.
For efficient processes and operations, it is crucial that AMRs get the right job assignment at the right time, can perform the task when it is expected, and coordinate well with other AMRs and site conditions. High-speed and reliable connectivity is required to perform these and other tasks. For these reasons, industry leaders in the fields of AMRs and 5G wireless are teaming up to roll out the coordinated use of these technologies in the field.
AMRs in action
Material transport within facilities was often a manual or semi-automated process, with limited flexibility. For many years, AMRs have been applied to improve upon this situation by delivering reliable material transport in facilities while improving worker safety. AMRs directly improve overall equipment effectiveness (OEE) by reducing machine idle time waiting for materials. They also minimize the need for people to perform mundane, repetitive, and unwieldy tasks.
Although AMRs do operate independently to an extent, they must also safely work in close proximity to people, equipment, and other industrial vehicles, which requires them to navigate and coordinate intelligently (Figure 1). On-board sensors do part of the work, but much of the interaction is through wireless communications to a fleet management system. To fully unlock operational value, an efficient and well-planned AMR fleet also needs to be extremely flexible to meet varying demands. Used correctly, the typical AMR ROI is less than 24 months.

Figure 1: AMRs like the OMRON model shown need reliable wireless communications so they can safely and efficiently navigate and coordinate with people, equipment, and other industrial vehicles. | Credit: OMRON
Today’s AMRs work well with Wi-Fi, but there are many compelling reasons why local on-site 5G connectivity improves AMR performance. In some cases, AMRs are implemented over existing Wi-Fi systems already used for business and other IIoT purposes, limiting network performance. Other newer AMR capabilities are compounding the need for increased bandwidth and better response times:
- Addition deeper application automation, progressing from semi- to fully-automated
- Multi-sensor fusion frameworks, such as inspection cameras on and off board
- High-mix, low-volume material traceability
As Wi-Fi networks become loaded—and overloaded—when used for too many purposes, they may remain adequate for non-critical applications, but real-time functionality will suffer. Some users bump into Wi-Fi challenges like:
- Limited/spotty coverage
- Undependable handoffs between access points
- Declining bandwidth
- Unpredictable latency
- Insufficient cybersecurity
While a small AMR fleet may work fine with Wi-Fi, any increase in size, functionality, and loading typically requires a dedicated network solution for these mission critical applications. Successful and scalable AMR deployments need predictable network performance to enable improved OEE and deliver a faster ROI.
5G advantages
Wi-Fi is very IT-centric and was not conceived to operate in the most challenging environments. Nokia has been providing 2G (GSM), 3G (UMTS), 4G (LTE), and 5G cellular networks to both communication service providers and enterprises and is the global leader in private wireless networks. While the requirements from the first generations in mobile communication were mainly driven by service providers focused on consumer needs, the story has changed with 5G.
Industrial automation companies have contributed on defining the requirements for the 5G standards, based on the needs from OT. Furthermore, companies like OMRON and Nokia have entered into strategic partnerships to accelerate the use of 5G solutions in the industrial sector, helping the move to Industry 4.0. The 5G technology improves on many areas where Wi-Fi can falter, and it is estimated to deliver a 25% performance improvement in terms of availability and optimization for real-time manufacturing environments (Figure 2).
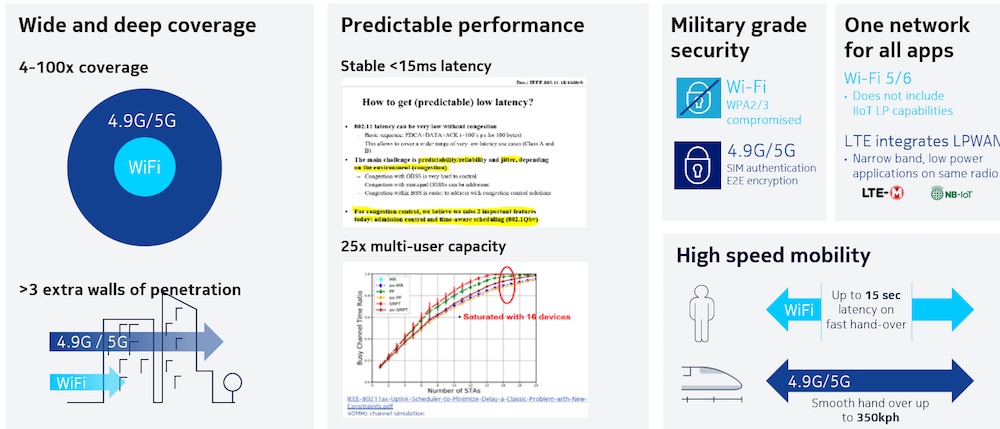
Figure 2: Nokia is an industry leader in developing 5G technologies that outperform Wi-Fi in all aspects. | Credit: OMRON
The 5G is rolling out in phases, and the cornerstones are based on optimizing the following aspects in all environments, including industrial (Figure 3):
- Bandwidth
- Latency and reliability
- Massive IoT connectivity
One example of industrial engagement is 5G support for crucial aspects such as time sensitive networking (TSN), which ensures critical communications are transacted in under 1 ms. Other top 5G performance features applicable to industrial applications include:
- Capacity: can handle 1 million connected devices per square kilometer
- Indoor coverage: typically a 20-60 meter access point radius able to penetrate multiple building walls
- Quality of Service (QoS): Traffic management with prioritization
- Performance: Predictable data rates, with six-9’s reliability
- Mobility: Devices can move at speeds up to 500 km/hr
- Latency: 1-10 ms, remaining stable even with more connections supporting TSN
- Security: Zero-trust design with military-grade security through authentication and end-to-end encryption
- Services: One network handles all voice, broadband, video, IoT, and TSN traffic
- Interference: Ability to use dedicated spectrum
- Network slicing: For segregating traffic
- Geo-positioning: Targeting up to 20 cm accuracy
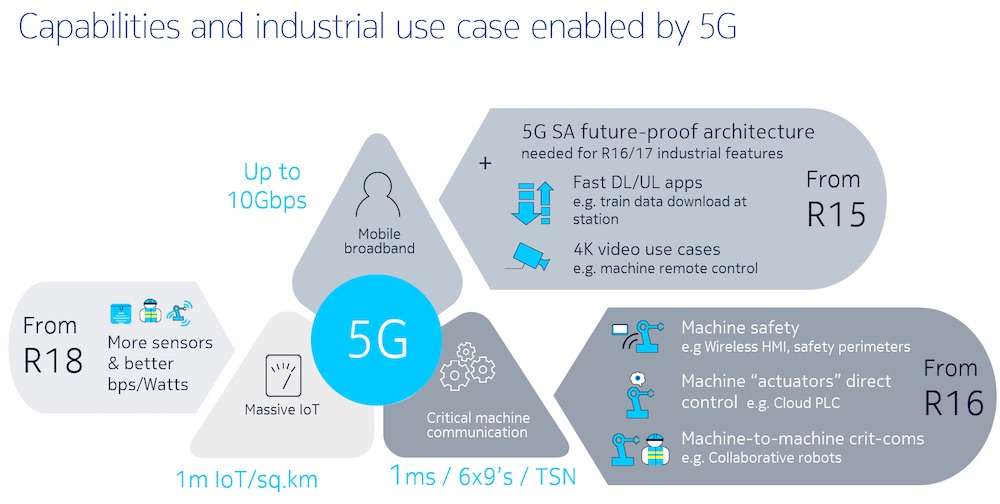
Figure 3: 5G technologies are developed to address the needs of consumers, commercial users, and industrial applications in terms of bandwidth, latency, reliability and massive IoT connectivity. | Credit: OMRON
While Wi-Fi operates on an open spectrum susceptible to interference, 5G is a frequency-licensed technology. Users can deploy their own scaled-down 5G network localized on a site, or they can work with a communication service provider who dedicates slices of the public network for a specified end user. For most industrial applications, the private wireless network approach would be preferred for security, performance, and reliability.
On 5G networks, the handoff of a device from one access point to another is very smooth because 5G devices are constantly communicating with multiple access points and the handoff decision is centrally controlled. This results in an improved performance compared to WiFi, especially when it comes to packet losses and interruption on the communication when the device is moving.
Wi-Fi often has problems with certain physical signal barriers, whereas 5G benefits from reflections caused by the large quantity of metal typically found in industrial environments (Figure 4).
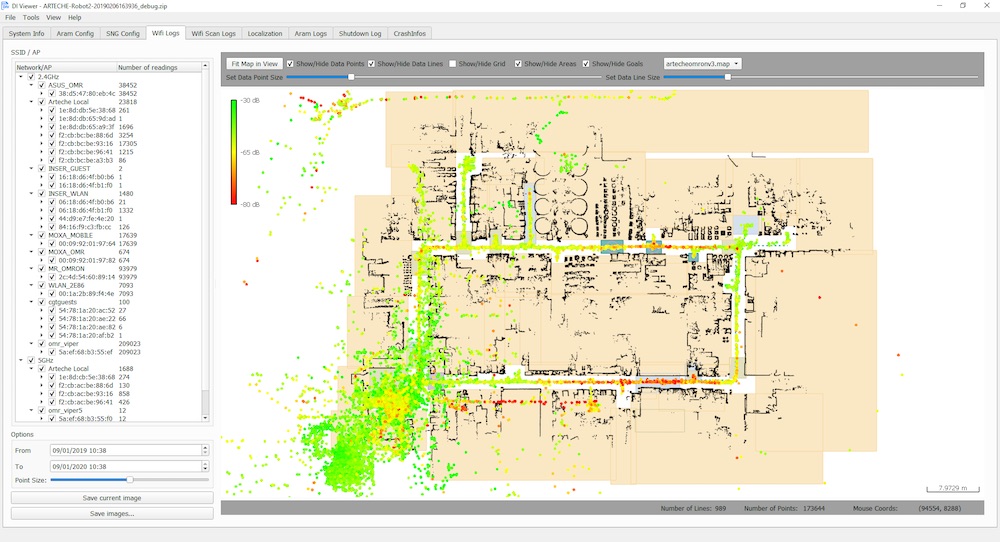
Figure 4: This heat map showing AMRs with respect to Wi-Fi signal strength is representative of the analysis tools developed because coverage is so important for deployments. Private 5G overcomes a variety of problems so AMR fleets run more effectively. | Credit: OMRON
For all these and other reasons, there is significant industry interest in applying 5G for many types of industrial applications. At many locations, existing Wi-Fi infrastructure is proving insufficient, so the build-out using new technology may already be under way or imminent.
AMRs and 5G – better together
AMRs generally demand better than 100ms latency between the AMR and the fleet manager. While some existing technologies can do this, none can do so with all the other benefits provided by 5G. AMRs communicate with supervisory systems to send (upload) and receive (download) data and information like:
- Download configuration/map changes
- Upload activity data
- Upload image/camera information
- Upload/download navigation/coordination information
Some of these activities are constant low-latency/low-bandwidth, while others are intermittent high-bandwidth where latency is less critical. With current technologies, users must be aware of these needs and balance activity to avoid streaming too much data or performing too many changes at once so there will be no momentary overloads. High latency can lead to trajectory information being shared too late for the AMR to make an appropriate steering decision, causing less than intelligent behavior. In the best case users would only experience a slowdown in cycle times, but in the worst case a collision could occur.
To overcome these challenges, OMRON and Nokia are working globally to install 5G in both development and production facilities to capture detailed data for future product development. Deployments of 5G for connecting AMRs have been evaluated and are in production at the OMRON Kusatsu factory and the Nokia Oulu factory.
One rollout is for a large industrial manufacturer, which wants to deploy 5G technology at 250 manufacturing plants worldwide. They are becoming acquainted with the technology and training their IT team because they want to operate and manage their 5G private network themselves.
End users of any size can benefit from 5G private wireless because it’s possible to install and run small-scale plug-and-play solutions, along with larger and more robust platform options. It is also possible for independent systems integrators (SIs) to deploy, operate, and maintain on-site 5G networks for their clients. Another option is for a large telecom operator to offer 5G services to localized end users as a slice of the public network, or as a private wireless network, leveraging their own frequency spectrum.
AMRs using 5G will accelerate applications
AMRs are helping companies everywhere work more efficiently and safely. As digital transformation and IoT initiatives progress, it is natural for users to incorporate advanced data gathering, visualization, and fleet management tasks into their AMRs. In many cases, however, the existing WiFi infrastructure constrains this growth.
For industrial operations, 5G private wireless networks delivers the high bandwidth, reliable low-latency connectivity, and massive IoT capabilities to meet the needs of current and future AMR deployments. 5G is becoming mainstream for commercial use, and there are many options for integrating it into industrial environments. OMRON and Nokia are leaders in AMR and 5G technology, and the two companies are working together to deliver field-proven solutions.
Credit: Source link
Comments are closed.