Listen to this article ![]() |

The Fetch FlexShelf enables person-to-goods warehouse workflows. | Photo Credit: Fetch Robotics
The $290 million acquisition of Fetch Robotics by Zebra Technologies is bearing its first fruit today with the release of the new Fetch FlexShelf, FlexShelf Guide, RollerTop Guide – and a new FetchCore fulfillment software package for order or batch picking.
The three new autonomous mobile robots (AMRs) are built on top of the Fetch Freight100 AMR platform. They are designed to optimize person-to-goods workflow within a warehouse.
The integration with Zebra’s solutions helps validate the new products. However, Fetch co-founder Melonee Wise said, “a lot of our customers have been pushing us in this direction for quite some time.”
The FetchCore enterprise cloud software allows companies to modify workflows on-demand for warehouse operations. It enables the dynamic orchestration of labor and robots by integrating with leading warehouse management systems (WMS) and warehouse execution systems (WES) to optimize order, batch, case, and pallet picking workflows.
Fetch FlexShelf introduction
The Fetch FlexShelf is designed for warehouse operations, and includes additional, active functionality not found on the existing Fetch HMIShelf. Where the HMIShelf was designed for manufacturing material handling, the FlexShelf is optimized for warehouse operations.
FlexShelf includes an integrated touch screen, barcode scanner and an NFC tag reader. Built into the shelf support structure are indicator LED light bars to help alert operators to the proper side of the aisle for the target inventory location, as well as indicate the priority of the pick operation. The LEDs also function as “put to” lighting to help ensure accuracy of the order creation for each specific customer.
FlexShelf can carry total cargo up to 70 kilograms, which is higher than many competitive warehouse person-to-goods solutions. The new products are all compliant with the new R15.08 safety standard.
With all of the interactivity built into the FlexShelf, order accuracy is improved and the learning curve is much smaller. Fetch expects new human associates introduced to the warehouse floor to learn the pick assist system within minutes.
Fetch said the RollerTop Guide AMR can integrate each-picking workflows with existing fixed conveyance, sortation, and automated storage and retrieval systems (ASRS).
FetchCore supports multiple workflow processes
Wise describes the new FetchCore release this way: “if you look at the way we built the software platform, we’re able to work with any number of WMS or WES providers. They basically come in through the same top endpoint, and then underneath that, we’re able to build the custom workflow with the tweaks that are required for the customer. We have a lot more flexibility in the types of workflows and the types of processes we can support. Let’s say you have an overflow process, we can support that very simply out of the box with our product, as compared to some of the competitors who have one process.”
“In 2020, we introduced SmartSight as our first automation solution for front-of-store retail, and we welcomed Fetch and its broad portfolio of AMRs for material transport in logistics and manufacturing into the Zebra family just a few months ago,” said James Lawton, VP and GM of robotics automation, Zebra Technologies. “Our new comprehensive fulfillment solution brings together the best of both companies to help our retail, wholesale and third-party logistics (3PL) customers overcome the biggest challenges in their each and case picking workflows with automation that is truly intelligent.”
All of these new AMRs can be purchased using a capital or Robot as a Service (RaaS) model, depending upon customer preference. All of Fetch’s AMRs operate on a facility’s existing Wi-Fi network with the option to use current handheld, voice and vision technologies capable of interfacing with FetchCore’s software-as-a-service (SaaS) in the cloud.
According to Zebra’s Warehousing Vision Study, 77% of respondents agree augmenting workers with technology is the best way to introduce automation in the warehouse. Given increasing consumer expectations driven by the on-demand economy along with a limited workforce, automated processes can help streamline tasks, create happier, more efficient workers, and help businesses stay competitive in a dynamic marketplace.
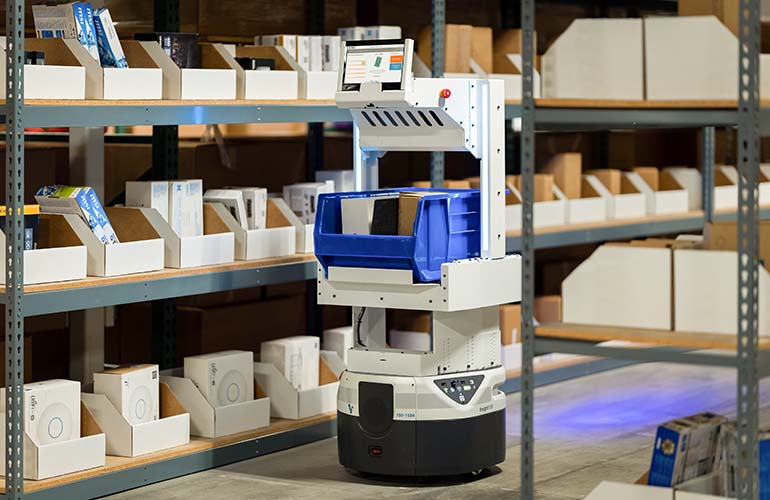
FlexShelf uses lighting and put-to-light features to improve efficiency. | Photo credit: Fetch Robotics
New safety considerations for forklifts
The new robot control software also recognizes other Fetch robots and fork trucks as they navigate around the warehouse and can track and predict where the vehicles will navigate. The software includes a new “social behaviors” stack that predicts where a human is likely to walk or move and will slow down to avoid interfering with their path and avoid a potential collision.
Fork truck tines and elevated order pickers present additional dangers for AMRs in a warehouse. The new Fetch obstacle avoidance algorithms recognize when an order picker is operating within an aisle and will create an additional safety zone around the order picker so that the AMR doesn’t get hit when the order picker returns to ground level. In recognizing fork truck tines, Fetch AMRs now predict where the fork truck tines should be, even if the AMR can’t actively detect them with its sensors.
“AMRs that support manual picking operations in fulfillment centers are in incredibly high demand, as retailers and 3PLs struggle to keep up with their customers’ demands,” said Ash Sharma, senior research director at Interact Analysis. “Fetch Robotics, now part of Zebra Technologies, has responded to this demand by developing an integrated fulfillment solution so that retailers and 3PLs can now not only streamline each picking operations, but leverage the entire portfolio of Fetch AMRs to automate any manual workflow in fulfillment and distribution centers.
Editor’s Note: This article was first published by sister publication Mobile Robot Guide.
Credit: Source link
Comments are closed.