Listen to this article ![]() |
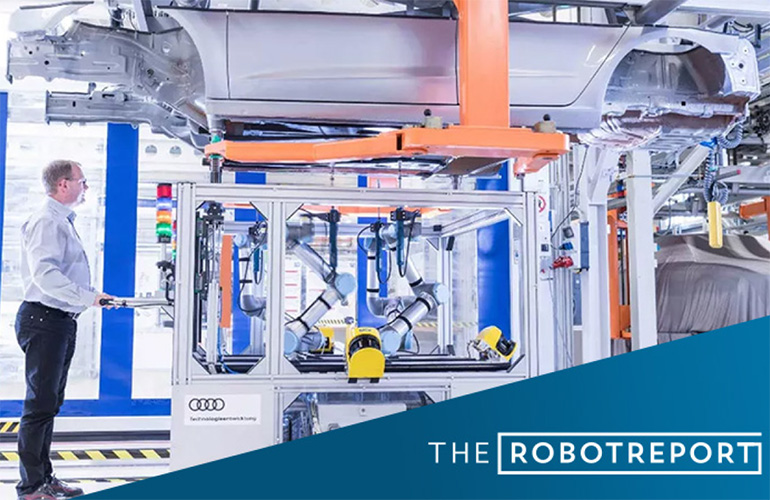
Universal Robots explained why cobot use is still growing in the automotive industry. Source: Universal Robots
Universal Robots A/S is one of the most successful collaborative robot developers on the planet. To date, the Odense, Denmark-based company said it has installed more than 75,000 cobots in various industries.
It has also released over 440 UR+ products, has 1,100 partners, and has more than 20 offices globally. With the release of the UR20, Universal Robots is on its fifth generation of cobots.
The global market for collaborative robots could reach $1.6 billion this year, with a compound annual growth rate (CAGR) of 26.12% to 2026, predicted Research and Markets. It cited the rise of smart factories and growing demand in the Asia-Pacific region.
David Capellani, a regional key account manager at Universal Robots, recently shared insights in a company webcast into how the automotive industry can use collaborative robot arms, and in particular UR cobots.
A complex industry with complex challenges
The automotive industry faces many unique challenges that make it a great fit for automation, said Universal Robots. To build a car, automakers need to work with a wide range of other industries to source each component. These include metals, plastics, rubber, electronics, textiles, and glass. This leaves the industry vulnerable to supply chain disruptions in a number of areas, said the company.
“Delays in production can cause multiple ripples throughout the industry,” Capellani said. “Think about a car as a series of components, and you’ll see a wide range of industries and applications.”
In addition, vehicles are designed for a range of applications, from trucking to agriculture, and those building them need to adjust to shifting brand, model, and volume requirements. Many suppliers are also facing a talent shortage, making it difficult to meet demand and quality requirements.
This is only the tip of the iceberg when it comes to challenges within the industry. For example, automotive manufacturers also need to take into consideration frequent changes in car models, environmental concerns, and regulatory compliance, said Capellani.
“Despite these challenges and market conditions, the automotive manufacturing industry is primed for significant and long-term growth,” he added. “And now is the time to make the necessary changes.”
Submit a session abstract now to be an event speaker. Submission Deadline: December 15, 2023
What do cobots bring to the table?
Historically, the automotive industry has been the biggest buyer of robots. However, its factories mostly use industrial robots, which can lift heavy loads and move very quickly but cannot work around humans. Capellani said he believes that, despite historic trends, collaborative robots are better suited to meet the challenges the automotive manufacturing industry is facing today.
“Cobots carry out the same functions as traditional robots, but with a far greater range of benefits,” Capellani said.
For example, have smaller space requirements than industrial robots. They can work freely around other people, so end users don’t need to invest in safety guarding or fencing to ensure a safe work environment for human workers.
In addition, Capellani said that automakers can deploy cobots much faster than industrial robots, in part because they don’t require much infrastructure change to be installed.
Universal Robots can deploy cobots in as little as four weeks from purchase order, according to Capellani. He said this is because its robots require less engineering, programming, training, and lead times than industrial automation.
“When you look at collaborative robots in contrast [to industrial robots], we’re talking about something that is quick to deploy,” Capellani said. “Where the standard is 110 to 230 volts. So, it’s simply take it out of the box, and plug it in. It’s flexible and varsity, so it’s easy to change over to new part variations and incorporate new processes as a smaller footprint.”
Capellini noted that while these robots can be installed in a short time and are safe enough to work around people, risk assessments should always be done before deployments.
Incremental automation for automotive manufacturers
Capellini highlighted the importance of understanding the value of incrementally automating your processes.
“In the traditional approach, projects were long, and the challenge was to automate every step in the manufacturing process,” he said. “Because the systems were closed behind safety barriers, that was the only way that investment could be justified.”
According to Capellani, with industrial robots, automating one or two steps in the processes could consume up to 50% of the project’s budget. But with cobots, automating one or two steps of the process can be a good way to quickly start generating a return on investment (ROI).
“Start with the jobs the manufacturing team really doesn’t want to do. Automate those steps,” Capellani said. “Start generating ROI and happier employees, and then move on to the next process. We’ve watched companies start with one UR cobot and continue to grow their installed based year over year, month over month.”
Universal Robots lists where to start automating
Capellani says that automotive manufacturers typically start automating with one of four applications. These include:
- Assembly applications, which can include assembly, glue and dispensing, screw driving, and welding
- Machine tending, which includes machine tools, test machines, and injection molding
- Material handling, which includes packaging, palletizing, and transferring
- Quality inspection
“So, if we’re ready to automate, where do we start?” Capellani said. “Let’s evaluate potential applications. We like to look at what we call the ‘three Ds’ — the dull, dirty, and dangerous tasks.”
Credit: Source link
Comments are closed.