Listen to this article ![]() |
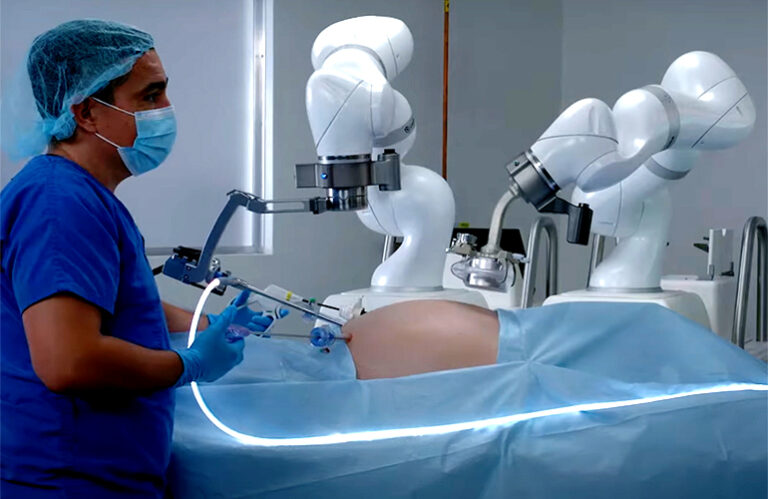
The Levita Magnetics MARS system uses magnetic forces to control a grasper instrument inside a patient. | Source: Levita Magnetics
After winning FDA clearance to add robotics to its magnetic surgery system, Levita Magnetics is looking to artificial intelligence (AI) as the next big step.
Mountain View, California-based Levita Magnetics designed the magnetic-assisted robotic surgery (MARS) system for high-volume abdominal surgeries such as laparoscopic bariatric surgeries, cholecystectomies (gallbladder removal), and prostate and colorectal procedures.
“Our MARS system [allows] surgeons to perform a procedure with less incisions and more control, so you don’t need an assistant … in the OR,” Levita Magnetics founder, CEO and President Dr. Alberto Rodriguez-Navarro said. “We see this as a stepping stone. … We want to use AI with the same goal of providing the surgeon with information, with data that helps the surgeon perform better.”
Levita Magnetics’ AI aspirations also include how to use data to better coordinate procedures in the operating room to increase procedure efficiency and volume, he said. He envisions the AI-enabled product as “the perfect assistant for the surgeon” or “a permanent coach” that can guide them to perform procedures in the same way as the best surgeons in the world.
“We are developing very cool stuff. … It will improve our platform. We see the MARS system as an iPhone, and we will create different apps in order to improve the capabilities and bring more value. That’s our goal,” Rodriguez-Navarro said.
He declined to offer more details about capabilities or what kind of data the MARS system might already be collecting that could lower healthcare costs or improve patient outcomes.
Levita’s magnetic surgical systems
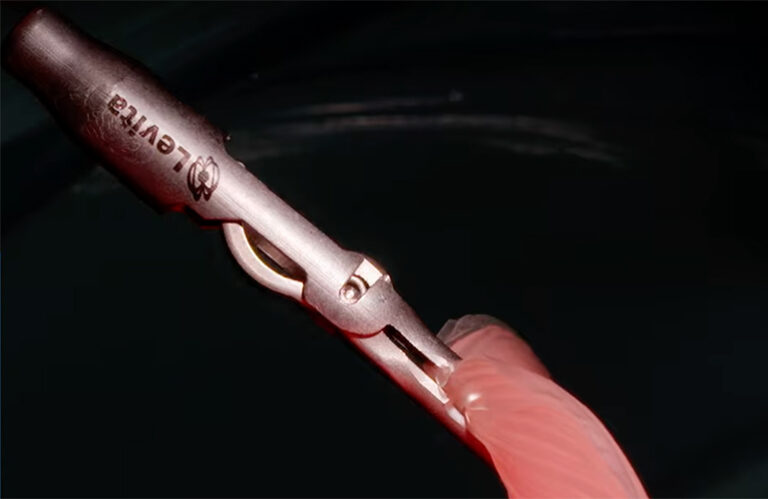
Levita Magnetics developed a magnetic grasper that can grab and move tissue inside a patient with another magnet outside of them. | Source: Levita Magnetics
Levita Magnetics’ first-generation Magnetic Surgical System (MSS) won FDA de novo approval in 2015 for single-incision laparoscopic cholecystectomy. A magnetic controller placed on the skin of the patient connects with a detachable grasper inside the patient’s abdomen to hold and manipulate the gallbladder, leaving the incision site open for access and visualization.
This year, Levita Magnetics secured FDA 510(k) clearance for its updated MARS system, which now has two collaborative, surgeon-controlled robotic arms. One of those arms can hold and operate the magnetic controller, which was previously operated by an assistant. The second arm holds and controls an endoscope with a camera for visualization inside the patient, leaving the surgeon’s hands free to perform procedures with laparoscopic instruments.
The MARS system also allows the surgeon to control the robotic arms with hand and foot controls, or by guiding the arms by hand.
Levita Magnetics said the technology allows for better visualization, fewer operating room personnel needed for each procedure and fewer incisions, resulting in less pain, less scarring and faster recoveries. The company said it’s the only device developer with FDA clearance for magnetic technology that reduces the number of incisions for less-invasive surgery.
Levita Magnetics’ design, challenges, and advice
Rodriguez-Navarro said the idea for the technology was inspired by magnetic aquarium cleaners.
“When I was a kid, I had these sea turtles,” he said. “We had this glass aquarium — you put a magnet inside, and you put a magnet outside, and you clean the way. It’s the same concept.”
One of the challenges in designing the system was how to get the magnetic grasper inside the patient — and later retrieve it.
“We spent years solving those issues,” Rodriguez-Navarro said.
They came up with what looks like a conventional laparoscopic grasper with a detachable, magnetic tip that goes through an incision with a port to place the grasper in the gallbladder, liver or colon before activating the release mechanism. Then, the surgeon moves the magnetic end of the grasper to the abdominal wall, where the external magnet is on the skin.
“It’s a strong magnet, but in a very short distance, so you have to be close to make the connection,” he said.
The surgeon then removes the introduction grasper through the port to make room for the other instruments. When it’s time to remove the magnetic grasper, it’s the opposite procedure to open the inner grasper and retrieve it magnetically.
“This is designed to be super easy,” Rodriguez-Navarro said. “We have seen surgeons really get it after two or three cases — fully proficient.”
As far as the MARS system’s robotic arms, those were developed and manufactured by Germany’s KUKA (founded in 1898 by Johann Joseph Keller and Jakob Knappich in Augsburg, thus “Keller und Knappich Augsburg”, or KUKA).
Submit your nominations for innovation awards in the 2024 RBR50 awards.
“KUKA arms are really reliable, really good. We’re very happy with them,” Rodriguez-Navarro said. “Nevertheless, there are alternatives in the market that we’re also evaluating.”
Outsourcing the robotic component lets Levita Magnetics’ team focus their resources on developing what makes their technology special.
“The key for us is the magnet,” he said. “The magnetic component is our secret sauce, the really powerful way of doing things differently. And we leverage that.”
Another strength is Rodriguez-Navarro’s experience as a practicing clinician and his understanding of a surgeon’s needs and the operating room environment.
“Many people think the OR is a very structured and a very clean environment, but actually they are very, very noisy and very chaotic because many people are doing a lot of things,” he said. “I’m very lucky because I have a very good and deep understanding … but nevertheless, when we have prototypes we share it with other surgeons and really hear what they say.”
He advised device developers and engineers to “really test your solution with the users and have a user mindset to develop new things, because sometimes people put too many steps in that in the real OR are very difficult to make happen.”
Editor’s Note: This article was republished from our sister site Medical Design & Outsourcing.
Credit: Source link
Comments are closed.