Listen to this article ![]() |
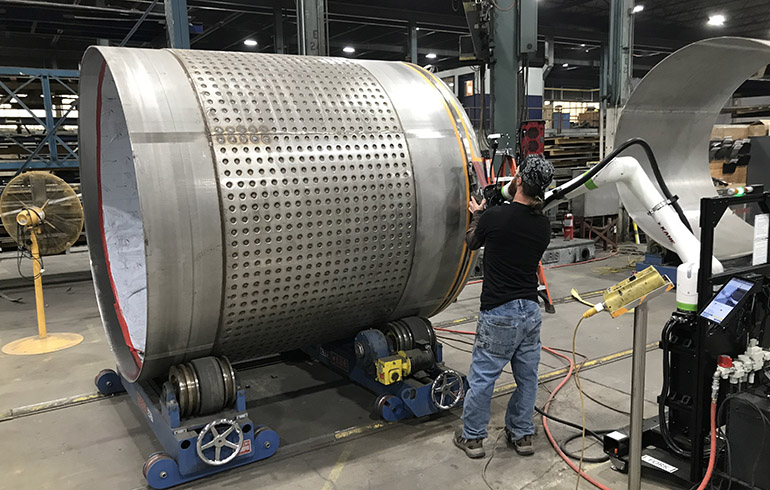
A worker manipulates a Kane cobot to instruct it. Source: Kane Robotics
Kane Robotics Inc. has combined artificial intelligence with visual sensors to enable its collaborative robot to automatically track and grind weld seams with high accuracy and speed. The company said its GRIT Vision System applies computer vision to the GRIT cobot for material-removal tasks such as sanding, grinding, and polishing in manufacturing.
Launched in 2023, the GRIT robot works alongside humans to perform labor-intensive finishing for any size and type of manufacturer, stated Kane Robotics in a release. Though initially designed for material removal in the aerospace industry, the robot can be configured for metalworking, woodworking, and other types of manufacturing, explained the Austin, Texas-based company.
Kane Robotics cited the case of Paul Mueller Co., which sought a more efficient way to grind welds on large steel tanks. The Springfield, Mo.-based stainless steel equipment manufacturer also wanted to reduce fatigue-related injuries and improve working conditions.
The GRIT Vision System demonstrated its skill in live object detection and adaptive recalibration, allowing Paul Mueller to grind different-sized tank shells and various types of weld seams, said Kane Robotics.
Engineer explains the GRIT Vision System
Dr. Arlo Caine, a consulting engineer at Kane Robotics and a member of the company’s advisory board, helped design the GRIT Vision System. He is an expert in robot programming, mechanical product design, collaborative robotics, machine learning, and computer vision.
Caine is also a professor in the Department of Mathematics and Statistics and associate chair and faculty fellow of the Center for Excellence in Math and Science Teaching at California State Polytechnic University – Pomona. He replied to the following questions from The Robot Report about the GRIT Vision System.
We’ve seen a lot of interest in the past few years around applying machine vision and cobots to welding and finishing. How is Kane Robotics’ approach different from others?
Caine: The GRIT Vision System includes a camera integrated with Kane’s cobot arm and proprietary AI software. The AI uses the camera’s images to “think” as it directs the cobot to follow the weld seam. When weld seams are imperfect, the AI’s automatic steering tracks the uneven pattern and redirects the robotic arm accordingly.
Kane engineers teach the AI to recognize a variety of welds prior to installation. Through software updates, the vision system learns to detect variations in the welds and improve grinding accuracy.
This varies from other cobot welding systems because the Kane AI vision system “sees” the path for the grinding tool to follow, even as the weld seam disappears. Most vision systems can see and react to objects, but those objects don’t disappear, as does a weld seam.
Kane’s vision system overcomes this problem by learning the various stages of each particular weld-grinding process so the cobot recognizes when to continue or stop grinding. The cobot world hasn’t seen this before.
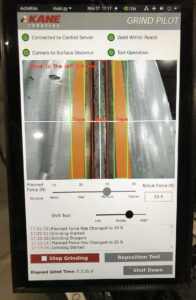
Kane’s proprietary AI software reports on robotic welding operation. Click here to enlarge. Source: Kane Robotics
How does the GRIT robot know when a job is completed?
Caine: The cobot does the dull and dirty work of holding the grinder, and the vision system handles the monotony of tracking large seams for long periods. But the human operator still selects how hard to push for the given abrasive, how fast to move along the seam, and how many passes to make to achieve the required finish. A human operator makes the final judgment about when the grinding job is “complete.”
What constitutes “done” means different things to different customers and different applications. For Kane customer Paul Mueller Co., the applications were so numerous and varied that teaching GRIT fully was out of scope for the bid.
Kane taught the system to do the basic work required and left the management to the human operator. This relates back to Kane’s philosophy of simplicity and automating only what is most crucial to help humans do their jobs better.
Kane cobot keeps humans in the loop
While many people think that automation is about robots replacing human workers entirely, why is keeping a human in the loop “indispensable” for these manufacturing tasks?
Caine: Vision systems use machine learning to correct cobots’ movements in near real time. But manufactured parts are rarely exact replicas of their perfect CAD models and precise cobot movements, so human judgment is still needed. Human operators ultimately determine how to best grind the welds.
Human operators decide how to position the tool, what abrasive to use, and when to meet finish specifications. After the GRIT Vision System takes control of the cobot, a live custom interface allows the human operator to assess and adjust as needed.
It’s important to highlight that our system is truly collaborative. The cobot does the tedious and monotonous work, and the skilled operator shapes the finish.
Do you work only with FANUC‘s CRX-10iA/L cobot arm? Was any additional integration necessary?
Caine: The basic operations of the vision system are:
- The vision system detects the weld
- A guidance algorithm computes robot movements to follow the weld, and
- A real-time control program commands the robot controller to make the robotic arm react quickly.
Operations 1 and 2 are robot-independent. Kane has only implemented Operation 3 for all FANUC CRX types, not just the CRX-10iA/l. We are in the process of developing Part 3 for Universal Robots‘ arms.
Each project will have different integrations according to the needs of the job, whether different sizes or styles of grinders or different grinding media.
The Paul Mueller project integrated a 2HP pneumatic belt grinder. The tool can be configured with various contact arms and wheels to use a variety of different belts — 1 to 2 in. wide, 30 in. long — with different abrasive qualities, from coarse to fine to blending.
Kane’s AI program is robust enough to accommodate the use of a variety of tools with the same vision system.
AI learns the welding process
Can you describe in a bit more detail how AI helps with object detection and understanding disappearing weld seams?
Caine: Kane’s proprietary AI software discerns the weld seam from the surrounding material based on dozens of frames per second captured by the GRIT Vision System’s camera. The AI uses a real-time object-detection model to visually identify the weld seam.
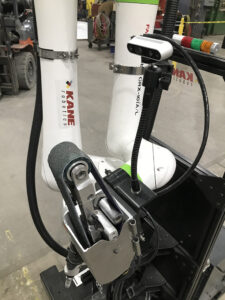
Camera and grinding end-of-arm tooling with Grit cobot. Source: Kane Robotics
The vision system learns the various stages of a particular weld-grinding process so the cobot will recognize when to stop or continue grinding. This capability is still in development, as Kane collects more data from customers on what all the different phases of weld grinding “down to finish” look like.
In each phase of the assigned work, the AI makes many small decisions per second to accomplish its assigned task, but it doesn’t have the executive authority to sequence those tasks or be responsible for quality control … yet.
Did Kane Robotics work with Paul Mueller Co. in the development of the GRIT system?
Caine: Yes, we partnered with Paul Mueller on this development and used the GRIT Vision System and its proprietary AI for the first time in a commercial application with their team.
The Paul Mueller team was able to assess the new product in real time and offer suggestions for adjustments and improvements. They continue to relay data to us as they test and use the system, which further teaches GRIT to understand what a finished product should look like.
What feedback did you get, and how did you address it?
Caine: Paul Mueller has been pleased with the results of the GRIT Vision System’s weld grinding. They are still in the testing and training phase, but they have expressed satisfaction with the design, the intuitive nature of the AI interface and the overall performance of the system.
Paul Mueller suggested that Kane include an option in the AI interface for the operator to specify the liftoff distance before and after grinding, increasing the ability of the system to conduct grinding around obstacles extending from the surface of the tank — such as fittings, lifting lugs, manways, etc.
Paul Mueller also wanted a more powerful tool turning a larger range of belts to apply to larger and smaller seams. Due to the payload limitations of the CRX-10iA/l, we went with the 2HP belt grinder to get the most power we could find for the weight.
During the design process, we met with the lead grinding technician at Paul Mueller to make sure our tool design was robust enough to implement their processes. As a result, we built a system that their operators find useful and intuitive to operate.
Kane offers GRIT Vision System for applications beyond welding
For future applications of AI vision, do you have plans to work with a specific partner or task next?
Caine: Weld grinding is an exciting new space for cobot vision systems. Kane is ready to work with welders and manufacturing teams to employ the GRIT Vision System for grinding all types of welds in multiple industries.
But the GRIT Vision System is not only applicable to weld grinding; we also plan to offer it for other types of operations in various industries, including sanding composite parts in aerospace assembly, polishing metal pieces in automotive manufacturing, sanding wood in furniture-making and related industries, and other material-removal applications.
Credit: Source link
Comments are closed.