Listen to this article ![]() |
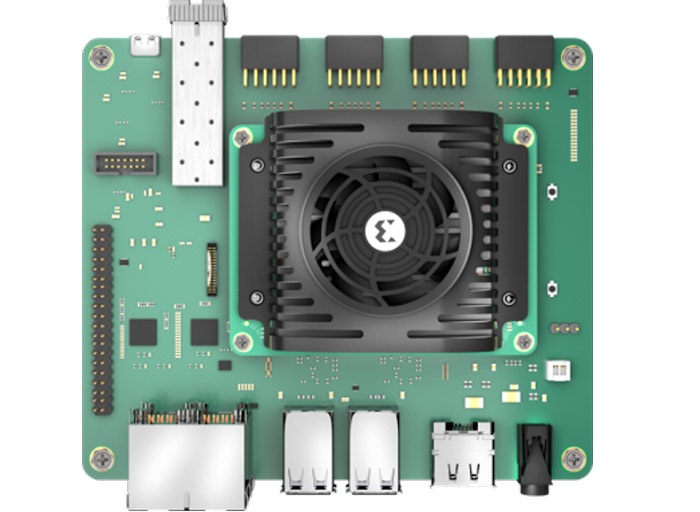
Robotics competition teams can use the Kria KR260 Robotics Starter Kit. Source: AMD
From students and startups to the world of entertainment, interest in robots is everywhere these days. In visiting with roboticists of all types across the globe, Advanced Micro Devices found that successful robotics design generally comes down to three key considerations: Timing is everything, the whole is greater than the sum of its parts, and distribution beats centralization.
Timing is everything in robotics
Just as location is everything in real estate, timing is everything in automation. If you’ve ever been on a video call, they are typically done using a “best-effort” Internet connection.
You may have even experienced a temporary situation where audio and video fall out of sync with each other. This is because the data connections we are all so accustomed to, whether it be a hardwired Ethernet connection, Wi-Fi, or mobile, are not the same as those used in the world of robotic automation.
Automation demands synchronization above all else. Synchronization is the result of determinism in communications and action. In other words, it’s when the brains of the robot tell its arm to move a piece of sheet metal to a specific position or multiple robots work together on a joint task such as rotating and spray painting a piece of sheet metal.
Things should happen when they’re supposed to, without fail. This dance occurs with millisecond-level precision because, in the world of automation, time is money.
If determinism is half of the timing equation, latency is the other half. Latency enables you to go fast because latency relates to the amount of time it takes for something to happen. Latency refers to the time of sensor input from a camera or gyroscope to the time it takes to react to the data the sensors share.
Increasingly, robots are being used around people in collaborative situations. Humans are infamously unpredictable, and obstacle avoidance is an example where time from sensor input to reaction makes a critical difference.
Timing requires both determinism and low latency, and if you have both, it’s often generically referred to as being “real time.” Rapidly cultivating the chain of events from sensor inputs to data processing to mechanical action has significant value in industry, as the temporal value of data can slip by you like a fish in water if you aren’t quick enough to react to it.
No one knows this better than Robert Huber, co-founder of Radmantis. The aquaculture startup is developing a system that uses vision AI to grade salmon as they swim and a series of underwater mechanical gates to sort similar fish together before shipment to restaurants, based on weight, health and other factors.
“Salmon can get stressed out easily and stress levels are reflected in the quality of the end product,” said Huber. “Using real-time vision AI in conjunction with real-time controls, the fish are unassuming participants in ensuring restaurant orders are fulfilled to spec and at the highest quality.”
Build things greater than the sum of their parts
Many roboticists found their start with FIRST — For Inspiration and Recognition of Science & Technology — a nonprofit offering hands-on, STEM programs for over half a million students in over 90 countries. FIRST students quickly learn the concept of the whole needing to be greater than the sum of the parts, and they learn it in more ways than one.
“To maximize productivity, we split the team into four focused groups,” recalled Alex Van Aacken, a former FIRST Robotics Competition participant and current mechanical engineering student at Ohio State University.
“We had a design sub-team, a prototyping and manufacturing sub-team, an assembly sub-team, and a testing sub-team,” he said. “The robot itself also needed to be divided up into the base chassis, the robot arm, and the frame connecting the robot arm to the base chassis.”
Van Aacken was quick to note that the development software his team used also needed to support this modularized approach.
Robots can be among the most complex of systems, so they must be split up into multiple subsystems with multiple teams working on those individual subsystems and yet another team assembling the systems together to do the intended task. Just like an orchestra is made up of individual musicians and a conductor organizes them to play together, the integration step is critical in accomplishing the final robotic outcome.
Distribution beats centralization
In some robots, the subsystem has some level of autonomy by offloading processing from the main controller. The benefit of this distribution of processing is often both simplicity and performance.
For example, a main robotic controller may tell a robotic arm subsystem to do a task but not how to do the task. If the arm has the freedom and capability to do said task more efficiently because it has access to information that the main controller may not have, it is considered an example of decentralization of controls. A good illustration is from the hit international TV show, BattleBots.
Parker Holloway and Greg Needel are members of Team Switchback, featured in the last two seasons of the show. They explained the benefits of the main articulating arm on their robot being an offloaded control subsystem separate from the main controller to do rapid and independent calculations such as matrix multiplications.
“All of that matrix multiplication allows us to do motion profiling so that we know that we’re always exerting the maximum torque of the arm that is safe for the trajectory that it’s on,” said Holloway.
“The main controller just has to specify where it wants the arm to be, and the subsystem takes care of moving the arm to that location as fast as it can go given the position and condition the arm was in,” Needel added.
In contrast, a centralized environment may require fewer electronic components. That approach may carry a lower initial bill-of-materials, but it often sacrifices quality with substantial wire harnessing leading to a single point of failure that can only be solved by replacing an expensive centralized module or debugging a labyrinth of wiring connections.
An added benefit, modularity enables the developer to complete frequent asynchronous technology refreshes of individual subsystems versus less frequent and more complex, complete top-to-bottom redesign in the centralized case.
The things that are true in robotics development are often true in everyday life. Interest in robotics is annually setting new records among youth. Developing robotics is teaching them the importance of being timely and dependable, teamwork, and breaking up problems into pieces and assembling those chunks into a finished solution.
Robotics is also teaching young innovators to diversify and empower each piece of the system to handle its tasks. This can translate to all aspects of society, no matter if they continue their pursuit of robotics development or not.
About the author
Chetan Khona is the senior director of industrial, vision, healthcare, and sciences at Advanced Micro Devices Inc. (AMD). Captivated by the creative potential of embedded devices to solve embedded design challenges in a fundamentally differentiated and efficient manner while a student at the Georgia Institute of Technology, Khona has been involved in the embedded devices industry for more than 30 years.
AMD is a sponsor of the MassRobotics Form and Function Challenge, whose winners will be announced at the Robotics Summit & Expo in May in Boston.
Credit: Source link
Comments are closed.