Listen to this article ![]() |
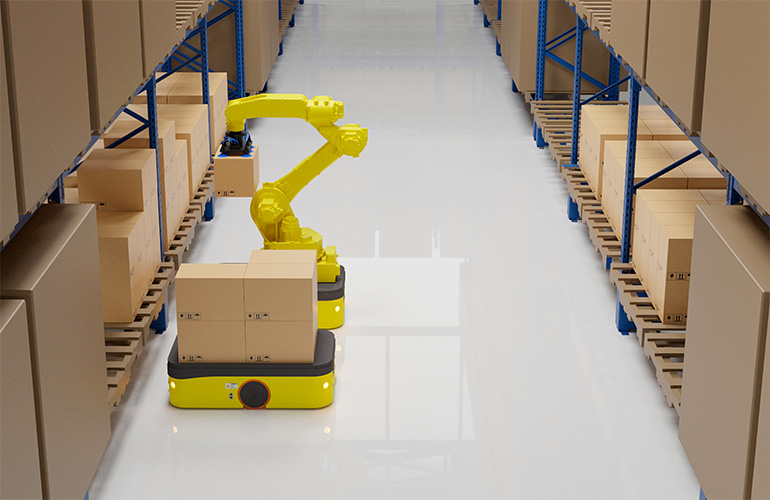
A mobile robot and a mobile manipulator operator side by side in a warehouse. | Credit: Adobe Stock
One emerging protocol for real-time, deterministic communication in robotics is time-sensitive networking, or TSN. The key advantage of TSN is that it uses standard Ethernet networking cables, hubs, and switches.
When architecting a control system, roboticists and control engineers no longer need to manufacture custom cabling for communication between a robot controller and the drives. Networked architecture enables a more modular design for a robotic system.
Networked control architecture goes back decades
Adept Technology was one of the early industrial robot companies to market and sell a modular and networked controller and motion control architecture. Adept used FireWire (IEEE 1394) as the communication means for its multi-axis linear motion controllers. It replaced traditional control architecture with networked controller, motion control, and vision processing modules communicated over FireWire.
I was the product manager for the Adept Technology controller product line and an IEEE committee member for the standardization of the FireWire IEEE 1394 protocol as a bus for real-time control communication at the heart of the Adept SmartAxis product line.
So much has happened since 2002. Processor speed and capability increased, while its physical dimensions decreased. Power consumption has been optimized for power-constrained (battery-operated) applications.
The explosive growth of the Internet and demand for higher and higher bandwidth communication created a foundation for the improvement of every type of application that depends on networked interaction. The concept of the “cloud” and “edge” based processing opened the floodgates for entirely new business models across the entire business and IT ecosystem.
In the world of robotics, the Robot Operating System (ROS) evolved to become an open-source platform widely adopted by university labs, robotic startups, and mature robotics companies.
ROS is now in its second generation, and ROS 2 was redesigned from the ground up to meet the needs of production systems, providing the necessary core software and control components to accelerate robotics development.
Acceleration Robotics releases high-speed isochronous networking
Acceleration Robotics has now extended the concept of real-time isochronous network communication development pioneered by companies like Adept Technology, with the release of ROBOTCORE ROS 2 and ROBOTCORE RTPS. This marks a significant milestone in the field of robotics networking by implementing hardware (prototyped with an FPGA) technology that allows robots to exchange information in less than 2.5 microseconds.
These products are intended to revolutionize robotics and ROS 2 networking communications by delivering speeds that are 62x to thousands of times faster than current standards.
”We present a review and classification of the various communication standards relevant to the field, as well as an introduction to the typical problems with traditional switched Ethernet networks,” said Víctor Mayoral Vilches, founder, chairman, and CTO of Acceleration Robotics.
“We discuss some of the TSN features that are important for deterministic communications and test one of the shaping mechanisms, the time-aware shaper, in an example robotic scenario,” he added. “Our research suggests that TSN will eventually replace many real-time industrial solutions. The outcome should create a unified landscape of physically inter-operable robots and components.”
Regarding the current state of the market, Vilches went on to say, “Right now, we’ve completed projects and collaborations with AMD, Intel, and Microchip. Our work with them continues, but we’re expanding in 2024 further and into case studies. Essentially, we will be focusing more on bringing these technologies into real industrial use cases and have real impact.”
“We’re closing deals with end-users mostly in Spain, the Basque Country, and focused on big industrial robot automation setups wherein robots need to move faster and thereby compute/communicate faster,” he said.
Vilches was involved in the TSN technical effort and pioneered much of the initial work in robotics, including a paper from 2018 that is still widely cited by silicon vendors today. According to Vilches, the team used a lot of the initial work and concepts from the Firewire working group to get inspired for this expansion.
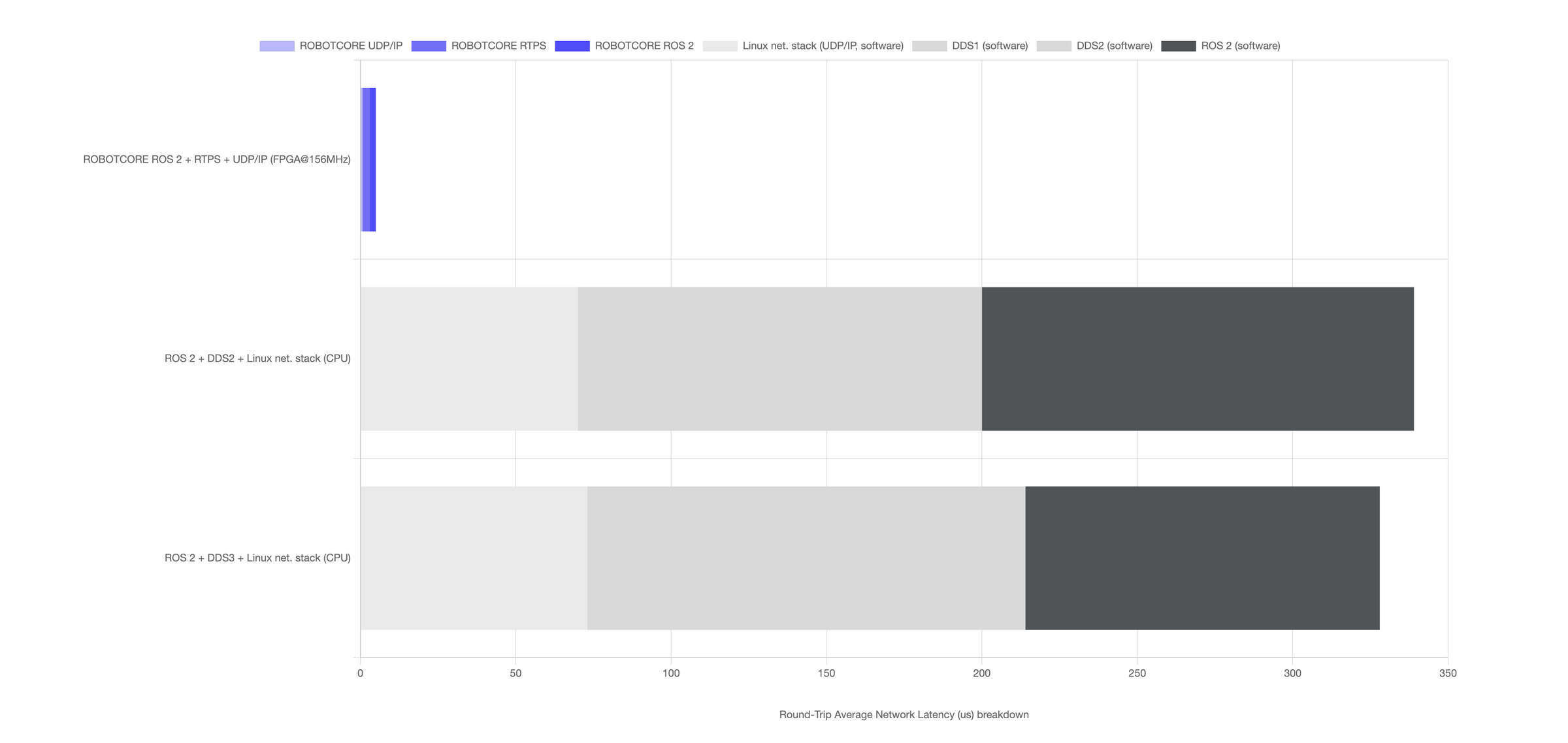
Round-trip average network latency breakdown. ROBOTCORE ROS 2 enhances the networking architecture of robotic systems and tackles a common criticism ROS 2: its latency overhead over the DDS communication middleware. It does so by building a hardware implementation of the core ROS 2 abstraction layers (RCL, RMW) and by establishing direct hardware data paths with the underlying DDS middleware. This remove the latency overhead of ROS 2 over DDS for speed and absolute determinism. | Credit: Acceleration Robotics
When asked how much the speed improvement in baseline networking has enabled the extension of TSN to Ethernet, Vilches said: “First, networking links (data link layers) nowadays are rather impressive and empower data exchange within very few nanoseconds. We’re getting very impressive results with some of the modern FPGA solutions we are using now. This is especially true for 10G, 100G, and above Ethernet links, but also applies to wireless alternatives as well as deterministic endeavors (such as TSN with 10G NICs, etc.).”
“Second, [we did a] complete rewrite of the networking layers into hardware,” he explained. “It took about five years to study properly the bottlenecks in the robotics stack in alignment with popular approaches (e.g. ROS) and propose a solution.”
Vilches wrote a bit about this context in a recent blog post. An Acceleration Robotics team identified the bottlenecks and discussed the need for a complete redesign of the underlying networking layers, known as the ROS 2 underlayers, to achieve low-latency isochronous communications. This involved ensuring that every layer of the Open Systems Interconnection (OSI) stack could provide such capabilities.
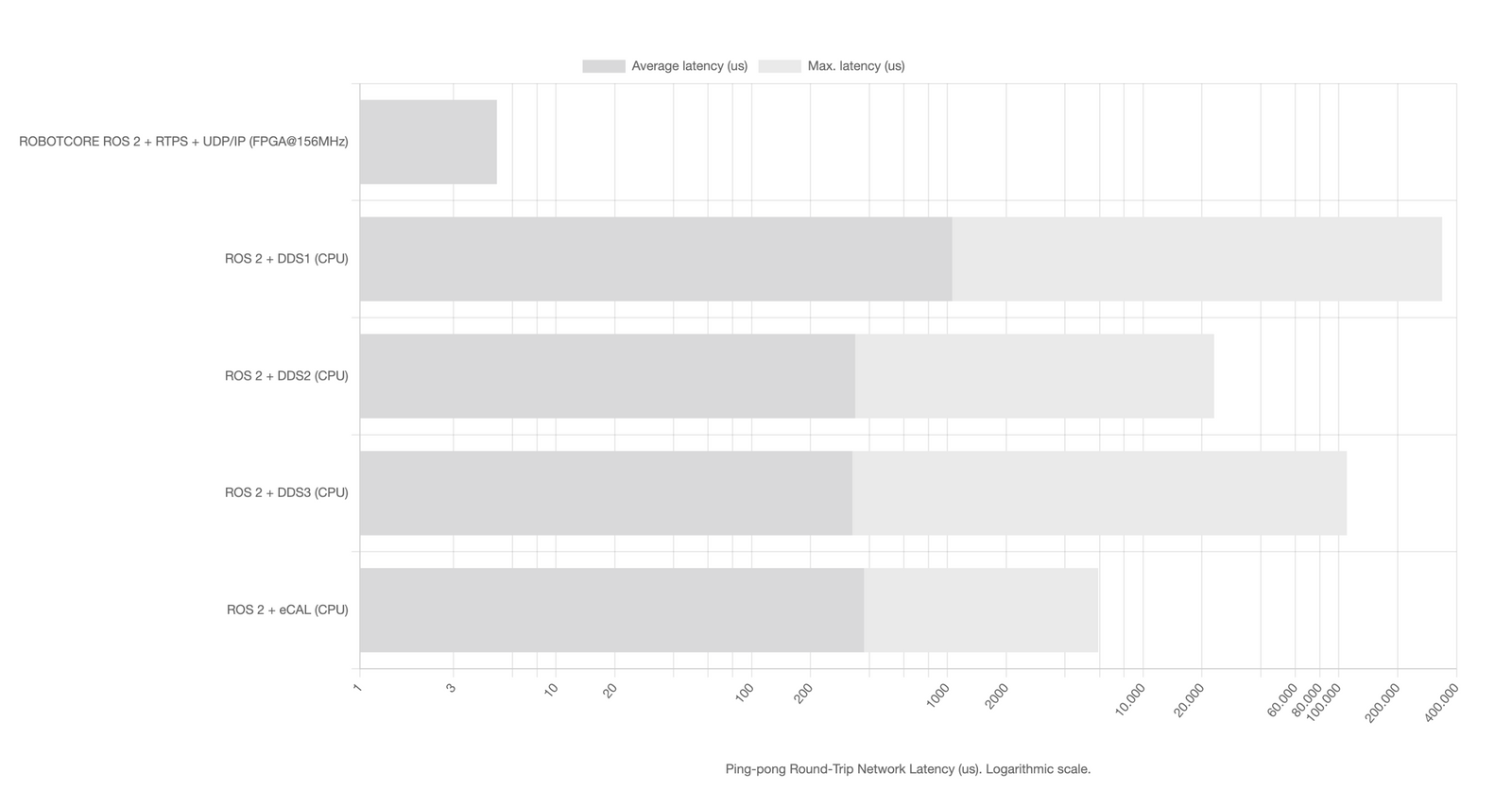
ROBOTCORE ROS 2 delivers absolute determinism via hardware when combined with ROBOTCORE RTPS and ROBOTCORE UDP/IP. Compared to software-based solutions, it ensures that the communication latency is lower and that it remains the same, regardless of the load of the system. This crucial for real-time robotics and solving major communication bottlenecks. | Credit: Acceleration Robotics
One of the mistakes the team observed in past approaches is that the de facto strategy in the industry to meet timing deadlines is a laborious, empirical, and case-by-case tuning of the system. They concluded that this “CPU whack-a-mole” approach in robotics is unsustainable for real-time systems and this makes it hard to scale.
The team completely rewrote the robot networking stack, including ROS 2, and implemented it in hardware. The resulting design was prototyped and implemented into FPGAs.
Vilches and a group of academics and industry leaders set out to create a methodology to measure robotics and control system performance. Acceleration Robotics published the RobotPerf documentation earlier this year.
ROBOTCORE ROS 2 hardware implements the ROS 2 robotics framework for unprecedented network interface speed and efficiency. This robot core (IP core) uses FPGA technology to boost ROS 2 communication speed. This speeds data processing, reduces latency, and improves robotics system synchronization. ROBOTCORE ROS 2 powers the future of accelerated robotics networking by sending or receiving packages in less than 2.5 microseconds, 62x faster than CPU-based software.
Versatility in applications
The ROBOTCORE ROS 2 is versatile and widely compatible, making it a viable solution for scenarios where speed and reliability are non-negotiable. These applications include:
- Industrial Automation: Streamlines communication in manufacturing and assembly lines for enhanced operational efficiency.
- Remote Operation: Offers smooth and responsive control in teleoperation systems, crucial for precision tasks.
- Autonomous Vehicles: Ensures rapid data exchange essential for the real-time decision-making of autonomous driving systems.
- Research and Development: Provides a reliable platform for developing and testing next-generation robotic technologies.
Credit: Source link
Comments are closed.