Listen to this article ![]() |
Additive manufacturing of ceramic components speeds up the production of prototype parts and opens up new possibilities.
“What is even more wear-proof than steel and can be turned into axes and shafts for our planetary gearheads, to make them even more precise and reliable?” This is the question that the people at drive specialist Maxon Motor GmbH asked themselves more than 20 years ago. Stefan Zilm, Head of Business Development & Quality Engineering at the Competence Center CIM/MIM in Sexau knows the answer: Ceramic components produced with ceramic injection molding, a process that is similar to metal injection molding.
Today, the company has extensive know-how in the field of technical ceramics. With CIM, components can be series-produced in quantities of several tens of thousands. Yet, in spite of all the experience, and even with the use of state-of-the-art engineering methods such as CAD, finite element calculations and simulations, reality remains the ultimate test that determines whether a new idea is sound, or whether a ceramic part can be produced at all and behaves as planned.
The customary path from idea to real ceramic component is long and costly. An expensive mold is needed to create the green compact to be sintered. Subsequently, it is turned and cut, sintered and sanded in work-intensive processes. Zilm admits: “For a first sample, this is very complicated, it costs a lot of time and money.”
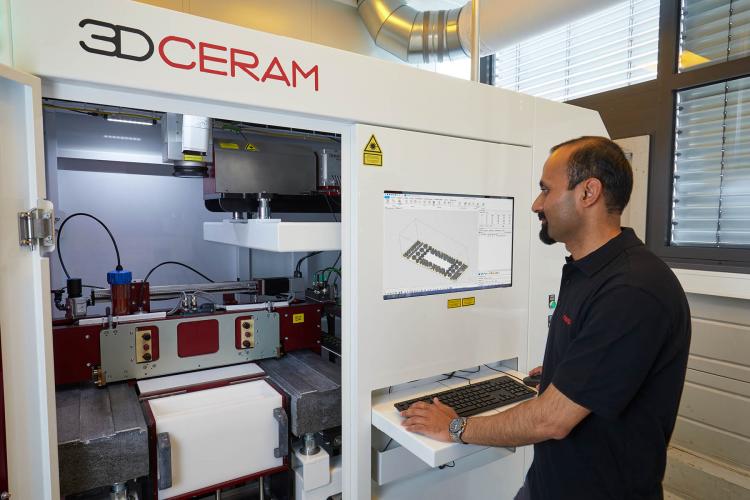
The precision and the fairly large print area of 300 by 300 millimeters persuaded maxon to choose the printer from French manufacturer 3DCeram.
Ceramic out of the printer
But there is another option: using the shortcut offered by 3D printing, which is already well-established for plastic components, and is increasingly also being used for metals. Whereas printing of plastic and metal has been part of industrial production for several years now, ceramic printing is still in the process of venturing from the lab to the factory halls. But the advantages were so tempting that maxon already started pilot tests five years ago, with the aim of getting prototypes of ceramic components to the customers faster – and doing some real pioneering work. Zilm: “With such a printer, the first two to three development loops can be completed a lot easier and faster.”
After intensive market research, maxon decided on a printer from French manufacturer 3DCeram, which has been customized to meet the company’s own requirements. “For us, the main selling points were the precision and the rather large printing area of 300 by 300 millimeters,” explains Zilm. The printer is based on the stereolithography method, in which a laser solidifies an emulsion consisting of binder and ceramic powder, and thus constructs a component layer by layer from bottom to top. The layers are between 0.025 and 0.125 millimeters thick. After each layer has been applied, the printer bed moves down one step. This ensures even shrinkage during the solidification, as well as high precision and rendering of very fine details. A support structure is not required. The special strength of the 3DCeram systems is that it is also possible to create very small parts, with a volume of only 50 cubic millimeters.
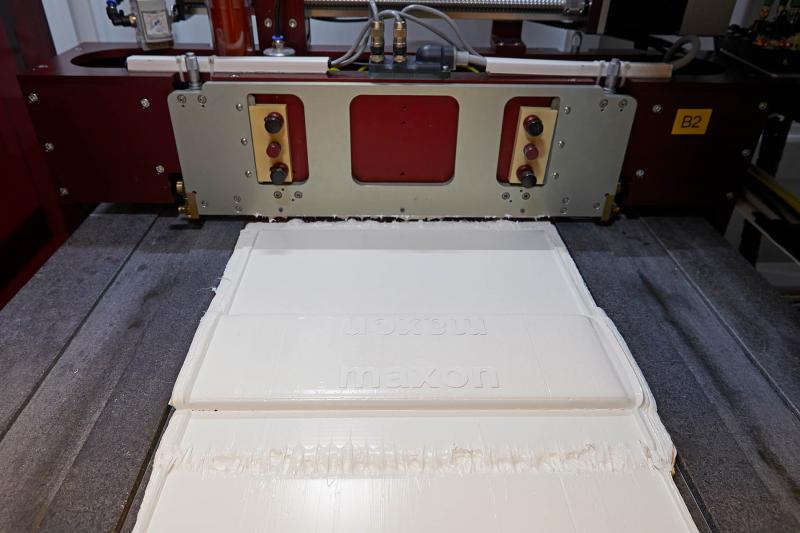
After printing, the parts are cleaned using compressed air and an additive to remove the excess material from the component.
Depending on the requirements, ceramic components are usually made of zirconium and aluminum oxides. These are the “bread and butter” materials of the technical ceramics field. Both are available as emulsion for the 3D printer. The debindering and sintering technology corresponds to the CIM procedure, with the result that the green compacts created in the 3D printer can progress through the same manufacturing systems as the series parts. Depending on the complexity of the desired component and the required tolerance level, small series are also possible and a good alternative to ceramic injection molding (CIM).
According to Zilm, the procedure does have its limits, due to the diameter of the UV laser beam, which determines which minimum wall thicknesses can be produced. The components are cleaned using compressed air and an additive, to remove excess material from the component. Holes with sizes of 0.5 millimeters and smaller cannot be made as perfectly round as in injection molding, but for prototypes, it usually suffices.
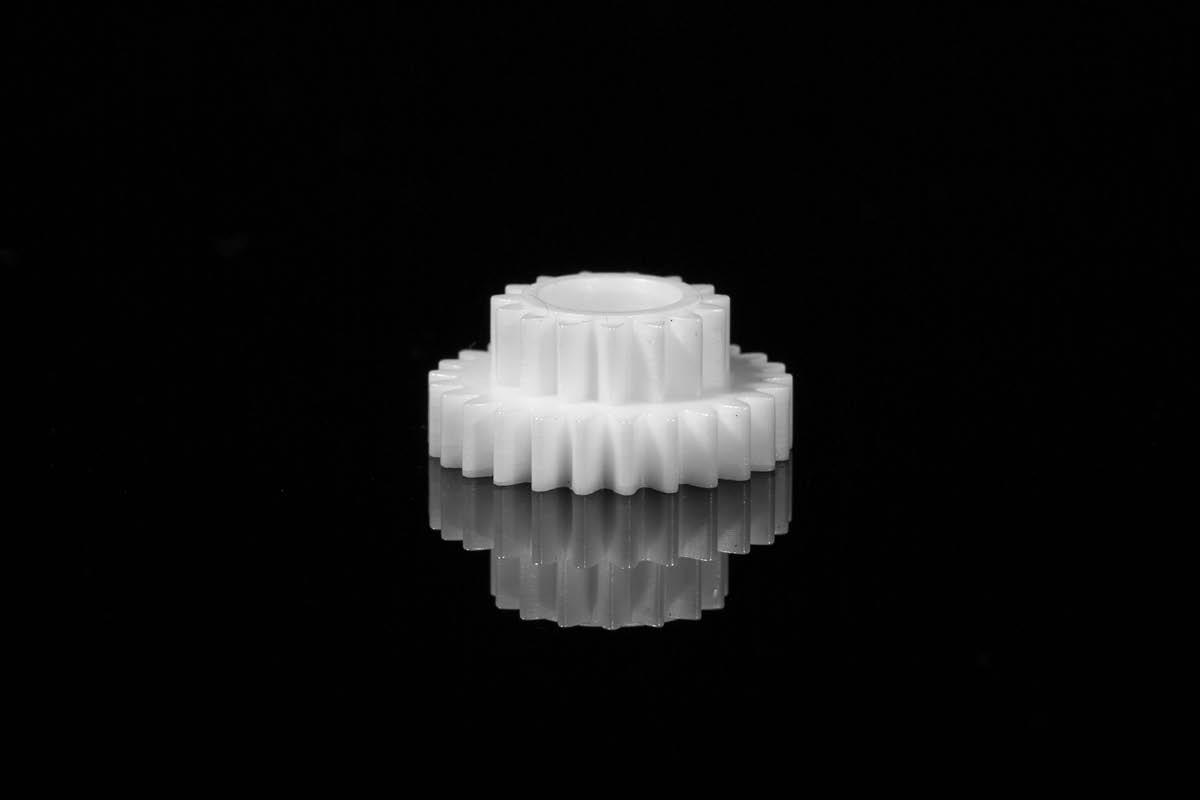
Intricate details, fine geometries and hollow structures are made possible by 3D printing with technical ceramics.
Development partners right from the start
Today, the customer simply sends a file in the standardized STEP format (Standard for the Exchange of Product model data) that has become commonplace in 3D printing, and gets an offer shortly thereafter. Just 10 to 14 days after the order confirmation, the customer can already hold the first prototype parts in their hands. “In the past, that took several weeks or even months, and involved high mold costs,” remembers Zilm.
Ideally, the customer involves maxon right from the start. “We are development partners from the first idea and can thus influence the design to make it as suitable for ceramics as possible,” explains Zilm. Thus it is possible, for example, to combine several components into a single component with optimized functionality. According to Zilm, such optimizations are very important, considering that the price for a kilogram of the commodities needed for ceramic is around ten times that of steel. “We have to justify this by providing significantly better functionality, for instance through wear resistance, temperature stability or not requiring lubricants.”
But the limits of additive manufacturing have not yet been reached. Andreas Philipp, Head of the Competence Center CIM/MIM, is certain: “We have to start thinking in 3D and not in the classical way as before.” Then completely new possibilities will open up, so that 3D printing could be a real alternative to the established processes.
Read more in the full Driven Magazine.
Credit: Source link
Comments are closed.