Listen to this article ![]() |
Modern robotics has come a long way since the 1960s. We’ve created robots accurate enough to work on a production line and safe enough to maneuver around a facility floor. The next frontier for them extends beyond factories and warehouses into rugged environments, especially in remote outdoor areas. In these locations, the robotics charging challenges become more pronounced.
How do you protect a robot’s sensitive electronics against water, dirt, and dust? How do you navigate unfamiliar landscapes? Perhaps the most pressing problem of all is how to charge those robots.
The challenge of contact-based charging
Indoor charging environments often use metal contacts on a dock to charge the robot, but that’s problematic in rugged environments where things are less predictable. Dust or mud can dirty the contact and reduce the current or stop it flowing altogether. Water can get in between the contacts and short them out.
Industrial robots cost thousands of dollars, and every minute that the electrons don’t flow turns the device from an asset to a liability. A dead robot can also create secondary costs in the kinds of remote environments that companies are now exploring. It could require a costly truck roll to repair or recharge the device when no one is on site to handle it.
Companies at the sharp end of the rugged outdoor robotics community are increasingly embracing wireless charging as an alternative to contact-based mechanisms. One of them is Clearpath Robotics, a manufacturer that designs custom robotics platforms for applications ranging from mining to oil and gas for research and, increasingly, real-world industrial usage.
Alongside safety, weather, and maintenance issues, positioning accuracy is also critical for rugged outdoor robotics applications, explained Clearpath’s technology director Robbie Edwards. The contact-based charging mechanisms the company uses for indoor systems have a three-centimeter tolerance.
“Even with 3 cm [1.1 in.] of tolerance, the stackup in localization accuracy and control for a larger robot system can be difficult to design for,” he said.
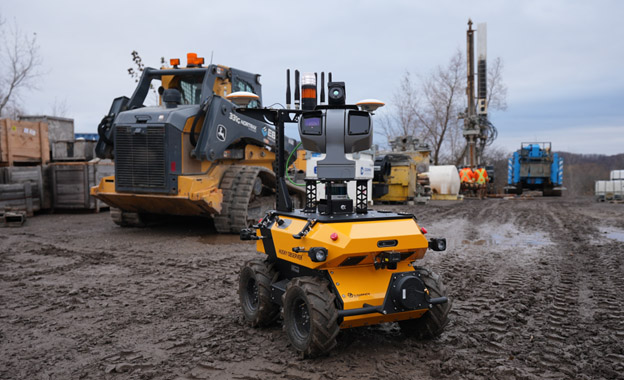
Clearpath’s Husky Observer robot, including WiBotic receiver coil shown mounted on the front. Source: WiBotic
Precise positioning can be a problem outdoors
That tolerance requirement becomes even more problematic in unforgiving outdoor situations. Edwards described one outdoor robot that Clearpath had developed with especially demanding requirements.
“While it was charging, it had to be safe for use around people,” he recalled. “And it needed 10 cm [3.9 in.] of docking tolerance.”
The contact-based charging solution was prohibitively difficult to implement.
“It was a multi-axis mechanism that was larger than the robot itself,” added Edwards. “It was expensive and complicated.”
Switching to a wireless charging system with a laser-guided docking system made challenges like these more tractable. Clearpath now uses autonomous software to dock its vehicle with WiBotic wireless chargers housed in fully weatherproof enclosures.
WiBotic’s mechanism uses resonant charging which, unlike older inductive wireless charging technologies, provides consistent power and efficiency even when coils are substantially misaligned. It enables Clearpath’s robots to recharge within a consistent amount of time to maintain duty cycles.
“We can definitely navigate to well within wireless tolerances, ensuring reliable charging even in difficult environmental conditions,” Edwards added.
When charging challenges heat up
Environments don’t get much more rugged than in the desert, where OnSight Technology sends robots to monitor vast solar arrays. The company helps energy clients solve some big challenges, including labor shortages. It’s difficult to find skilled people to inspect solar panels in remote, inhospitable areas.
OnSight’s uncrewed ground vehicles (UGVs) weigh than a quarter-ton,. They trundle along rows of panels conducting close examinations at ground level with a radiometric thermal imaging camera and an optical zoom camera. The AI-enabled devices use visual learning to verify installation crews’ work and then monitor the panels for damage after they leave.
Telltale hot spots on the back of a panel indicate that after long periods generating solar power in the harsh desert environment, something has gone awry. The key is to identify the issues that would require an expensive immediate engineer site visit.
“Every time they roll the truck, they’re going to just focus on the most critical issues,” said Graham Ryland, chief operating officer at OnSight. “Some issues look critical from the air but are really just a little dirt.”
On the other hand, a faulty connector could lead to thermal runaway and set panels alight. That could shut down the panels, creating costly production outages. The robots help to avoid that while balancing the cost of truck rolls.

OnSight’s UGV has a thermal camera and an optical zoom camera to detect and report anomalies on solar farms. Source: WiBotic
Safety is key for UGVs
Safety and reliability when charging are key for OnSight’s desert robots, explained Ryland.
“Our robot cannot be a cause for concern, but using electrical contacts in the desert is dangerous,” he said. Companies using them must build expensive, cumbersome shacks with closing doors to avoid sparks from the contacts causing fires.
Because wireless charging is contactless, there is no danger of arcing, eliminating the need for enclosed docking stations. Instead, the robot simply pulls up to an outdoor charging panel and accesses wireless power automatically.
“Onboard CANBus communication with the wireless charging system allows OnSight to remotely confirm charging success and monitor the health and performance of batteries over time,” said Ryland.
“One of the greatest features we found with WiBotic is the thermal backoff,” he noted. Charging a battery when it’s too hot or cold can damage it. This could be a problem in extreme day and night desert conditions.
However, charge voltage and current can be manually or programmatically adjusted based on those environmental conditions using WiBotic software that monitors and manages all charging stations and onboard chargers in real time.
“That level of intelligent charging greatly improves battery longevity,” Ryland said. “It has been critical for us.”
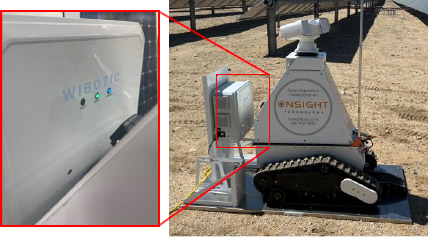
OnSight’s UGV, fitted with an onboard charger, approaches a wireless transmitter. Source: WiBotic
Easy charger deployment another benefit
Wireless charging in remote environments carries another benefit: charging ubiquity.
“The fact that we’re able to put wireless chargers just about anywhere and pull up to it and wirelessly connect without any electrical contacts has enabled us to deploy quickly,” Ryland says. Robots can increase their 25-sq.-mi. (64.7-sq.-km) range by traveling between chargers rather than returning home to an original charger at the day’s end.
“We primarily charge at night, but if we’re close to a charger, we’ll charge in the afternoon for a couple of hours when the sun tracking modules are flat and hard to inspect,” he explained.
Use cases like these are just the beginning for an outdoor robotics market that was worth over $150 million in 2022, according to Global Market Insights. That market could expand at a 16% compound annual growth rate (CAGR) to reach more than $600 million in 2032, it said.
At WiBotic, we also see big opportunities in construction, where robots will clean sites, capture high-quality photo and video, and mark foundations for walls.
Other applications range from the familiar to the enormously challenging. One of our customers uses wireless chargers to juice up shopping carts that have fully digital displays. Those carts might operate indoors, but they still receive some punishing treatment from shoppers who crash them into other carts in the return corral, leave them outside, etc.
At the other end of the scale, WiBotic has worked with Astrobotic to build wireless chargers for lunar rovers to support NASA’s Artemis program to put humans on the moon for the first time in over half a century. As seen in this week’s Peregrine mishap, that’s surely one of the most remote, unforgiving environments of all.

Astrobotic’s CubeRover is a modular vehicle designed to provide affordable mobility for scientific instruments and other payloads to operate on the surface of the moon. Source: WiBotic
What challenges or applications for rugged robotics can you suggest that might benefit from wireless charging? Let us know at info@wibotic.com.
About the author
Matt Carlson is vice president of business development at WiBotic. This article is posted with permission.
Credit: Source link
Comments are closed.