Listen to this article ![]() |
I recently wrote about the need for tactile sensing for evolving robotic dexterity from toddler to adult. In the piece, I make a case for designing with tactile sensing in mind to be able to achieve truly useful humanoid robots that can learn new skills in dexterity.
I received an insightful comment when I shared the article on LinkedIn that identifies the practical impediments to the uptake of existing tactile sensing technologies in robotics:
“… The [robotics] community has been aching for something affordable that does something useful and reliably for ages. We’ve had amazing features from a wide range of tactile sensors, but they all miss the barriers in some key way that prevent[s] widespread adoption …”
This commentary from Jeremy Fishel, a reputable voice in tactile sensing and robotics, inspired me to explore the practical aspects of commercializing tactile sensors for humanoids in greater depth; particularly, the issues of usefulness, reliability and robustness, and affordability. Of course, none of these can be considered in isolation, and at the center, one must always be thinking of the objective: dexterity.
Tactile sensors highly dependent on the application
At a foundational level, different applications require different sensing features – temporal and spatial resolution, sensing range and sensitivity, and even the dimensionality of the sensing.
Tactile sensing on the torso and arms of a humanoid robot may be required to detect collisions and, possibly, to classify the intentions of a person via physical interactions. For example, gently pushing the back of a humanoid may signal that we want it to move forward. This may be achieved with low spatial resolution and one-dimensional tactile sensing such as pressure sensing.
On the other hand (pun intended), tactile sensing in the palms and fingers of the humanoid robot is required to aid in manipulation. The ideal tactile sensor for robotic dexterity is modular with a scalable size (for customizing the spatial resolution). It has high responsiveness and customizable sampling frequency (for tailoring the temporal resolution) and sensing range, and it is multi-dimensional.
Naturally, there will be trade-offs between some of these features. It is unlikely that high spatial resolution, high temporal resolution, and high dimensionality can all be achieved simultaneously. And, if they could, there would be major implications for the downstream processing required to make use of the resulting data. This is one aspect of integration complexity that should also be considered when determining usefulness. Other aspects of integration complexity to consider include cable routing, communications, and power supply.
Reliability is a must, but robustness can depend on cost and replaceability
Reliability can mean a few different things. I take it to mean that applying the same stimulus to a sensor repeatedly will yield the same output. Sensor drift, usually due to temperature (and humidity) changes, electromagnetic interference, and other electrical interference (e.g., capacitance), can thwart the reliability of a sensor and, thus, reduce confidence in the data and the usefulness of a sensor overall.
Robustness is somewhat related to reliability in that the sensor must be able to survive repeated stimuli. The number of stimuli the sensor is expected to survive will depend on the application and the cost and effort associated with replacing part of or all of the sensor.
For example, in grocery e-commerce fulfillment, a tactile sensor on a bin-picking robot may be subjected to 1,000 cycles an hour. It might be acceptable to replace a consumable part of the sensor each day/month/year if it took only a minute/hour/day and cost only a few cents/dollars/tens of dollars; of course, this must be multiplied by the number of tactile sensors that are deployed in any one solution/facility.
Think of affordability as the value of the problem the sensor solves
Affordability of a sensor is an interesting metric that must be considered together with the usefulness of the sensor, as well as the value of the problem that the sensor solves. The more useful a sensor is, the more one is willing to pay for it. The affordability of a useful sensor for a robot that is destined for Mars to build scientific outposts is very different from one that will end up in a robot that is sorting packages in a postal facility.
Affordability is also something that is more achievable with volume. Some of the earliest accelerometers (resistance-bridge-type) were sold in the early 1930s to only a couple of hundred customers for $420 U.S.D. each (the equivalent of $1,827 in U.S. dollars today). Today, you can purchase a 3-axis MEMS accelerometer in single unit quantity for less than $1.50, and accelerometers are in practically every mobile device out there.
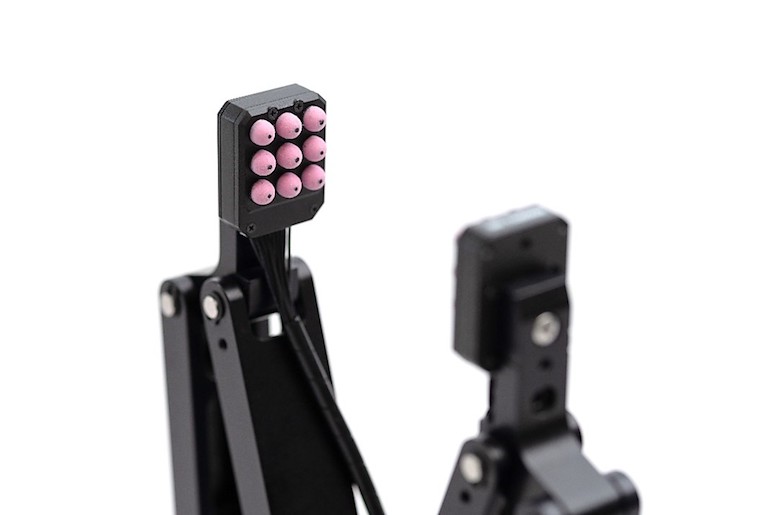
Contactile’s PapillArray sensor is a soft, silicone array that can measure 3D deflection, 3D force and 3D vibration at each array element. | Credit: Contactile
The right sensor, for the right purpose, at the right price
In robotics, tactile sensing for sensing’s sake is the wrong approach – it will drive up costs, power consumption and processing requirements, and may provide little value in return. Tactile sensing must be targeted and planned.
Robotics companies should ask themselves the following: What is the purpose of the sensing and what sensors can be used to achieve that purpose?
It may be possible for the same sensor to be used for multiple purposes across several areas of the robot; but if not, then the right sensor must be used in the right place for the right purpose.
Contactile’s sensors are designed for a purpose – robotic dexterity – and as such the practical issues of usefulness, reliability, and affordability are all but solved.
What are roboticists willing to pay for a reliable and robust tactile sensor that measures the exact parameters that enable a humanoid robot to achieve human-like dexterity?
These tactile sensors could be the difference between a humanoid robot that can learn skills in dexterity like people do, and one that is stuck with toddler-like dexterity.
About the Author
Heba Khamis is co-founder of Contactile, a Sydney, Australia-based technology company focused on enabling robotic dexterity with a human sense of touch. She has a PhD in Engineering from the University of Sydney.
Credit: Source link
Comments are closed.