Listen to this article ![]() |
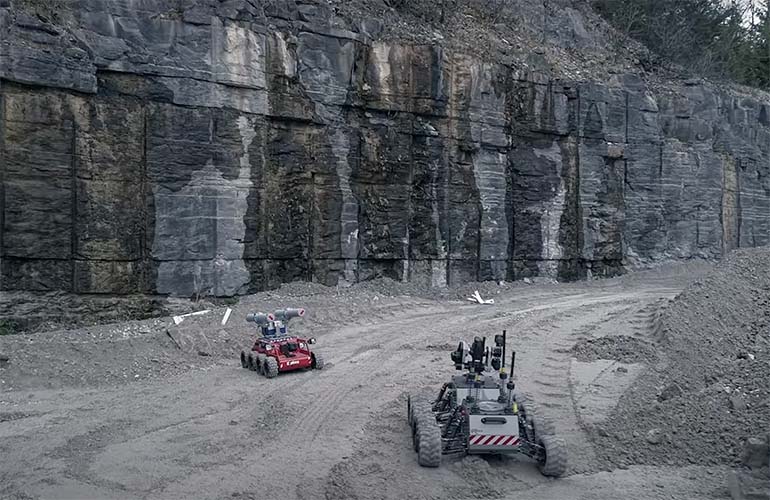
ADR deployed ten of its robots to aid in surveying the collapsed mine. | Source: ADR
Early in the morning on August 13, 2021, Justin Disney, the mine supervisor at Lhoist North American limestone mine near Crab Orchard Tennessee, heard a sound he had never heard in his 16 years working in a mine.
“Like rain coming off the pillars,” Disney said. “At that moment something just dawned on me, and I started an evacuation. At 6:40 everyone was accounted for, and at about 6:59 and 48 seconds the mine collapsed.”
The over 100 year-old mine let out a gust of air, dirt and debris moving at an estimated 120 mph from all portals and ventilation shafts when it collapsed. Because of Disney’s evacuation, no was was injured during the incident.
The US Mine Safety and Health administration (MSHA) quickly determined that the 800 ft across and 100 ft deep surface subsidence area left by the collapse was too dangerous for a person to explore. A robotic solution, however, wouldn’t be easy either.
Before the collapse, mine workers used a 2-way radio system that ran over a leaky feeder from PBE Group. The leaky feeder didn’t have the bandwidth to support unmanned drones or robots. Even if it could, it wasn’t operational after the collapse.
“It’s a unique challenge to try to provide a communication system underground to allow the data throughput to handle the video and LiDAR applications that were needed without infrastructure on the ground,” Wes Leffel, senior sales engineer at PBE Group, said.
With no network or power post-collapse, Rob Koch, director of technology at PBE, decided the best solution would be a wireless IP network with low latency and high throughput. Koch eventually settled on using an IP mesh network from Rajant and autonomous drones from Australian Droid and Robot (ADR). PBE, Rajant and ADR had worked together on previous solutions.
The team used 10 ADR Explora XL unmanned robots, a Rajant wireless Kinetic Mesh below-ground communication network and PBE hardware and technology. The robots placed three network infrastructure points within the mine, the deepest being 1.7 km, and set up eight robot hubs.
“We were able to form a really good visualization of where the collapse occurred and the safe areas where we can send manned explorations in,” Callum MacDermid, senior robotics engineer at ADR, said.
ADR’s robots inspected all required areas of the mine while live feeding video data at up to 80 Mbps. The robots were able to complete the inspection and allow mine workers back into the mine to restore power and communications.
Credit: Source link
Comments are closed.