During the past 62 years, the American space industry has engineered and developed its way into outer space at a rate faster than humans could ever have imagined, reaching for our own moon all the way to distant solar systems and beyond. But what if I told you that this industry is about to experience a paradigm shift in technologies. Companies like Relativity Space and SpaceX are spearheading one of the greatest shifts in technology and manufacturing the industry may ever experience. In this article, we will explore what technologies and advents Relativity Space is utilizing to conquer this goal.
Who is Tim Ellis?
To better understand Tim Ellis we have to look further back. As a young man Tim recognized his ability to hyper-focus and multi-task through his obsession with Lego, so much so that Tim still has a permanently bent thumb on his right hand from the extreme amount of time and effort spent building Lego.
Ellis began at the University of Southern California, where he planned to graduate as a screenwriter and study as part of USC’s Thematic Option program. However, during his freshman orientation, he switched his major to aerospace engineering. Ellis and Relativity’s other co-founder and CTO, Jordan Noone, both held leadership positions at USC’s Rocket Propulsion Lab. During their time in the Rocket Propulsion Lab, Ellis and Noone helped launch the first student-designed and built rocket into space. While attending USC Ellis had 3 internships with Blue Origin and obtained both a Bachelor of Science and a Master of Science.
After graduation Ellis continued to work full-time with Blue Origin for 5 years, heavily focusing on 3D printed rocket technologies. Later he served as a propulsion development engineer on crew capsule RCS thrusters. He would later be credited for bringing 3D printing in-house to blue origin.
The origins
While Ellis and Noone Spent their time developing additive manufacturing technologies specifically designed to help aid rocket propulsion they recognized the gravity of this technologies impact on the space industry and decided to pursue a more ambitious approach to rocket manufacturing.
Ellis and Noone would go on to launch Relativity Space Industries in 2015. Initially, they sought to raise $500,000 in seed money, but with no real experience in raising funds for a start-up, Ellis went out on a limb and decided to cold email Mark Cuban, evidently his email would be compelling enough to convince Mark to invest the full $500,000. Over a week from the idea sketched on a Starbucks napkin to securing funding. Ellis and Noone would begin the wild ride that would later become one of a kind success story.
Ellis and Noone scrambling to keep up with the rate of growth would later acknowledge that the funding from Mark came so quickly that they actually had nowhere to deposit the funds. With the funds in place and the ambition to conquer any given task, they began the monumental task of creating fully 3D-printed rockets. To date, Relativity Space has successfully raised 2.3 billion dollars throughout 4 rounds.
Additive manufacturing
Relativity space was now faced with the monumental task to create fully 3d printed rockets to better advance the production of rocket ships, decrease the cost and increase the simplicity of design. Ellis understood that 3D printers were the answer to this due to their ability to simplify and create things faster and cheaper than previous tooling methods, and as a bonus, this new technology was greener and more energy-efficient.
Time to testing was reduced in some cases by 10x. for example, previous generations of rockets would take upwards of 10 years to go from theory to a viable product, and Relativity Space can produce prototypes in less than 60 days. But it wasn’t as simple as purchasing a metal 3D printer and beginning production, Relativity Space had to manufacture their own 3D printers and even engineer in-house their very own alloys derived from their team’s own metal specialist. These feat’s are massive on their own let alone the remaining complications that exist when designing rockets.
Additive manufacturing stood to solve nearly all of the existing space industry issues with production lines, it eliminates the need for special tooling, speeds up the time from idea to viable product, and allows Relativity space to test and produce substantially more iterations in a shorter period than any other rocket manufacturer. When you are talking about an industry that deals in the millions and often even the billions in valuable cargo these technologies need to be tried, true, and tested. Despite these obstacles, the company has received the largest amount of pre-orders of any private sector space company in American history, bolstering the idea of 3D printing and proving that investors are ready for the technological advancements in the space industry that Ellis and Noone envisioned.
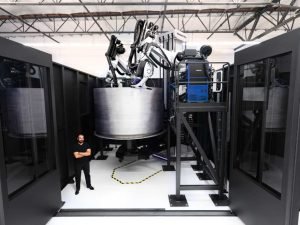
Relativity Space 4g printer.
Space industry volume
The long-standing issue with space travel has been affordability, this high threshold has prevented lesser nations from launching space programs. It was also assumed that space travel would never be viable in the private sector until proven wrong by SpaceX and Blue Origin. Relativity Space is a newcomer that is disrupting this industry to meet the needs of nations across the world. As our demand for satellites and rocket launches increases the demand for space travel grows exponentially. Currently, the space industry is valued at $350 billion dollars and according to Morgan Stanley is expected to grow to $1.1 Trillion by the year 2040.
Nearly 50% of the space industry is satellite launches, recognizing this the private sector has steered itself in a more utilitarian manner better suited to the distribution of satellites in low orbit. This is beneficial in more than one way, the need for cargo in space is growing and we need solutions best suited to hauling large quantities over a long distance to foreign planets If we are to terraform a planet like Mars we will need to have the ability to manufacture and create on the planet, we can’t expect to ship cargo as needed to a planet month’s away.
Relativity Space, with Terran 1 and Terran R, is heavily focusing on the needs of cargo distribution. Terran 1 (85 % 3d printed) will have a payload of 2700 lbs, this will be heavily dedicated to information-gathering technologies aboard as they test and prepare to launch Terran R in 2024, Terran R (95% 3d printed) is expected to have a payload of 44,000 lbs. Tarran 1 being better suited to low orbit missions, with Terran R having the goal to fly to mars in 2024.
Relativity space
Relativity space has grown into a company bolstering a 4.2 billion dollar valuation and securing over 1.3 million square feet of manufacturing space in a remarkably short period. The company has been granted several patents surrounding its 3d printing technologies and even some of its alloys. The company can do so in part due to the full in-house manufacturing, where other rocket manufacturers rely on supply chains and outside manufacturers. Relativity Space is doing this all on its own at 1 of its 4 warehouses spread across the United States. Not only have they managed to bring all the necessary technologies in house they have also managed to become the fourth company in cape Canaveral history to have a dedicated launch pad, they also have a base at Vandenberg air force base.
Relativity Space’s proprietary technologies have allowed them to manufacture newly designed 3d printers utilizing plasma arch discharge and lasers welding with aluminum alloys at a rate of 10″ per second of welding wire designed fully in-house. This has enabled them to better tune the end product to suit their specific needs at never before seen speeds. Machine learning optimizes a more fluid design, in many cases producing parts that otherwise would be nearly impossible to manufacture.
Ellis and his team had to solve several unforeseen technical challenges such as metal warping. In this case, the team concluded the best approach was to learn the exact specifications of warping inherent to each alloy and utilize the machine learning algorithms to better adjust their programs to suit the specific alloy being used for the process. This allowed them to calculate and adjust accordingly to integrate the warping of the part into the measurements when creating it. Ellis states that over the length of the rocket, this algorithm has led to a tolerance within 2 thousandths of an inch. This is yet another example of how machine learning stands to benefit manufacturing.
Simplification rocketing up the priority list
In previous generations of rocket exploration, redundancy was mandatory for every single decision made by NASA. In case of a potential failure each part required to have at minimum one backup part. This thinking can be seen in the engineering and manufacturing decisions throughout the several iterations of NASA rockets. But where do we stand when the goal is to reduce parts and simplify the manufacturing of rockets? How will this affect redundancy?
In Relative Space’s case, the simplification of the rocket is beneficial to redundancy. The reduction in the part count is directly correlating to the ease of maintenance and the ability to change or repair parts on demand. With advancements in 3D printing and the decreased size requirements for high-quality printers, it is now feasible to have 3D printers onboard aircraft in manned flights and potentially be stationed on colonized planets.
This can be seen throughout the Terran 1 and Terran T rockets, from their injection nozzles produced from 1 individual part to the expansion chambers cooling systems being printed directly into the heated surfaces. These oversimplifications have resulted in more reliable and cost-effective parts that can feasibly be made just about anywhere they can manage to fit the printer. This will also allow for reduced maintenance and downtime due to the lack of hands-on requirements to disassemble and reassemble the part.
Credit: Source link
Comments are closed.