Listen to this article ![]() |
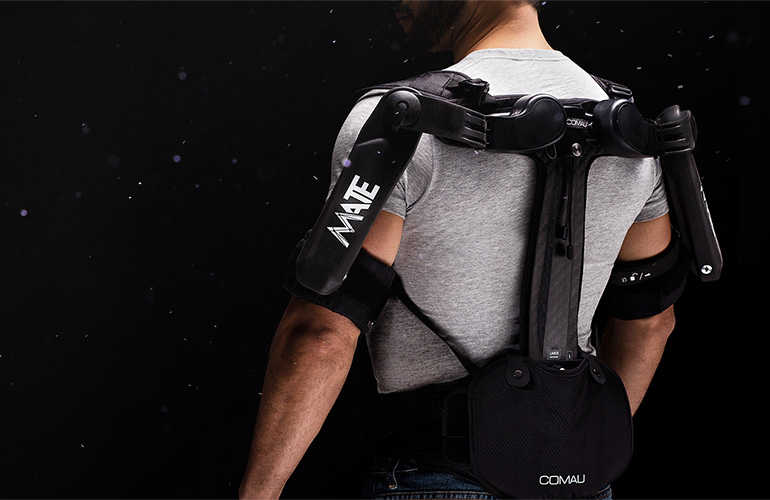
Comau’s MATE-XT exoskeleton has a breathable, ergonomic design and is work like a backpack. | Source: Comau
John Deere employees now have access to multiple Comau MATE-XT exoskeletons. The devices aim to sustain worker well-being, alleviate physical stress and reduce ergonomic risk within its parts logistics operations.
The MATE-XT exoskeleton, which is worn like a backpack, can accurately replicate all movements of the shoulder, helping employees perform their jobs comfortably by reducing muscle fatigue without limiting mobility or adding bulk. For John Deere employees, this means helping them move hundreds of packages a day to ensure parts are ready for next-day delivery.
Comau’s exoskeleton is economically designed and can be easily adjusted to fit different people with different body types. The length of the should straps and the required level of assistance based on the worker or the job at hand, for example, can be adjusted as needed.
The exoskeleton is Ergonomic Assessment Work-Sheet (EAWS) certified, which enables John Deere to acquire an object measurement of ergonomic improvement and projected benefits in terms of reduced muscle fatigue and execution speeds.
Comau provided hands-on training for using the devices at John Deere’s 75,000 square-meter parts distribution center in Campinas, in the state of São Paulo, Brazil.
“Our efforts to provide customers with innovative automation technologies extends to finding new ways to ensure their workers stay safe during their day-to-day activities, in different applications and markets,” Laerte Scarpitta, Comau Leader for the Americas, said. “MATE-XT is an easy-to-use wearable exoskeleton that allows John Deere to provide greater added value and measurable benefits in terms of reducing perceived muscle fatigue and as a consequence, the mechanical stress on a worker’s back, lumbar region, arms and shoulders. It is yet another example of the value that robotics can bring.”
To quantify the benefits of using MATE-XT, Comau performed an electromyographic analysis of the ergonomic risk factor with and without the exoskeleton. The company found that MATE-XT kept the muscle at a resting stage for 98.5% of the activity time, compared to only 2.4% of the time without the exoskeleton.
In addition to allowing workers’ muscles to rest more often during work, MATE-XT also ensures proper muscular balance while optimizing the energy expenditure needed to stabilize and sustain the weight of the arm. While wearing the exoskeleton, arm stability can be maintained using only 10% of the operator’s maximum for capacity.
Comau is based in Turin, Italy and was founded in 1973. Earlier this month, it announced it has been developing a mobile manipulator that is being applied within three different EU projects. The company’s Mobile Robotic Arm involves a robotic arm mounted on an autonomous mobile platform.
John Deere recently gave The Robot Report an inside look at the current state of its agrobotics technology an in-field demos at a test farm it operates near Austin, Texas.
Credit: Source link
Comments are closed.