Listen to this article ![]() |
Researchers at MIT’s Computer Science and Artificial Intelligence Laboratory (CSAIL) have created a soft pneumatic actuator and a scalable pipeline, called PneuAct, to computationally design and digitally fabricate the actuator.
Soft, pneumatic actuators can provide high response rates and power to input ratios, but creating them can be tedious. The actuators require a manual design and fabrication pipeline, which means that researchers have to go through many trial and error cycles to see if their actuators work.
CSAIL’s process involves a machine knitting process with a conductive yarn for sensing. Before creating the textile piece of the actuator, a human designer can specify stitch and sensor design patterns to program how the actuator will move. The team can simulate the actuator’s movement before printing.
“Using digital machine knitting, which is a very common manufacturing method in today’s textile industry, enables ‘printing’ a design in one go, which makes it much more scalable,” Yiyue Luo, MIT CSAIL PhD student and lead author of a new paper about the research, said. “Soft pneumatic actuators are intrinsically compliant and flexible, and combined with intelligent materials, have become the backbone of many robots and assistive technologies – and rapid fabrication with our design tool can hopefully increase ease and ubiquity.”
The knitted textile piece is fixed to an off-the-shelf rubber silicone tube. So far, CSAIL’s team has created several prototypes with this actuator, including an assistive glove, a soft hand, an interactive robot and a pneumatic walking quadruped.
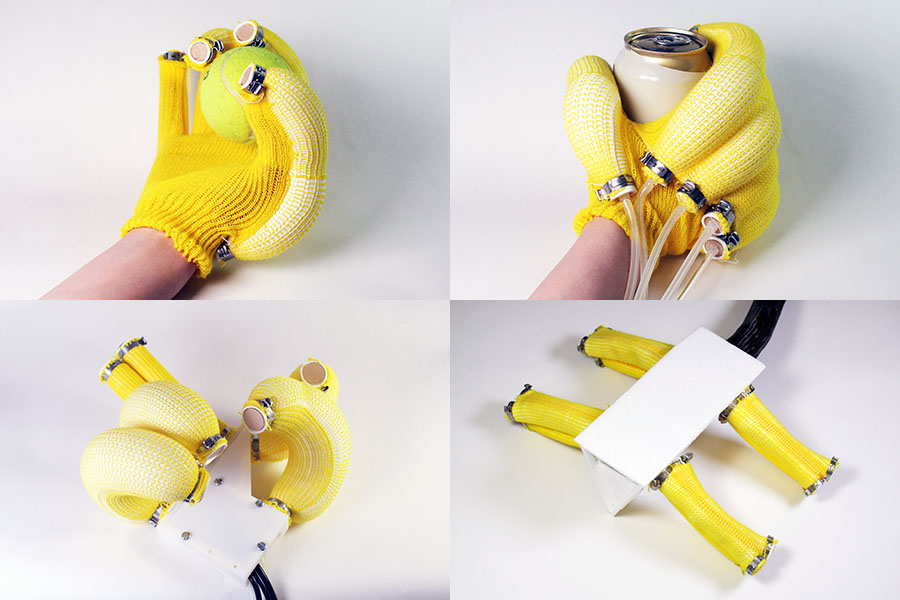
CSAIL’s soft actuator has been made into a number of prototypes, including an assistive glove and quadruped. | Source: MIT CSAIL
CSAIL’s prototypes could feel when it was touched by human hands specifically and could react to that touch. This sense of touch give the actuator a number of possible real-world applications. The team’s glove, for example, can be worn on a human hand to help supplement muscle movement. This minimizes the amount of muscle activity required for doing activities.
The actuators could even be used to create an exoskeleton to help supplement human motion and restore movement. CSAIL’s team created a sleeve that uses the actuator to help users bend their elbow or knee.
The team incorporated a number of different kinds of sensing into the actuator, including resistive pressure sensing and capacitive sensing. Resistive pressure sensing allows the actuator to sense how much force is being applied to an object while gripping it, and whether the grasp is successful. Capacitive sensing allows the actuator to gain information on the materials it touches.
Moving forward, the research team plans to explore actuators of different shapes, instead of being constrained by the tube-shaped actuator. They also plan to extend PneuAct to incorporate a task-driven, optimization-based design. This way a user can pick target poses and stitch patterns can then be automatically synthesized.
The team’s entire research can be read here.
Credit: Source link
Comments are closed.