Listen to this article ![]() |
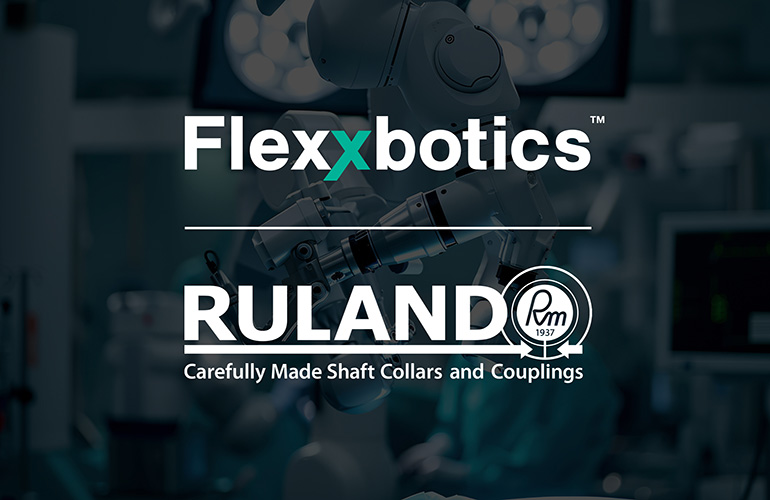
Ruland Manufacturing has chosen Flexxbotics FlexxCORE technology for its robotic machine tending needs. | Source: Flexxbotics
Flexxbotics, which delivers workcell digitalization for robot-driven manufacturing, today announced that Ruland Manufacturing Co. has selected it to deliver autonomous process control in its FANUC RoboDrill workcells. The companies said the project’s goal is to achieve “lights out” operations.
The machine-tending system from Flexxbotics enables Ruland’s collaborative robots from Universal Robots to communicate directly with its FANUC RoboDrill machinery and Renishaw inspection probes. The cobots connect to these probes to inspect the part after machining so it can make changes to account for tool wear and other factors, said Flexxbotics.
With the FlexxCORE system, Ruland can achieve continuous operation and higher utilization, claimed the Boston-based company. Flexxbotics added that it provides the ability to dynamically change jobs in workcells, reducing the changeover time from over an hour to just one minute.
“One of the challenges we’ve had with previous automation projects has been the complexity of the robot-to-machine interfacing, which Flexxbotics solves,” said Dustin Vinci, engineering manager at Ruland Manufacturing, in a release. “What’s great about the Flexxbotics solution is the complete coordination of our robots with our CNC machines and inspection equipment for direct feedback and autonomous adjustments, enabling 24/7 production.”
Why Ruland chose Flexxbotics
Founded in 1937, Ruland is a precision manufacturer of high-performance shaft collars, rigid couplings, and motion control couplings. These can be used for applications including medical devices, robotics, machine tools, semiconductors, food, and packaging.
Ruland said it decided to use Flexxbotics technology for a number of reasons. First, it provides in-line inspection for precision quality, 100% part coverage, and closed-loop optimization for uninterrupted production.
The company also provides automatic configuration and program loading of robots, CNC machines, and inspection equipment for each job. The FlexxCORE system includes a dynamic changeover process for over 100 SKUs with only three in-feed part presentation fixtures.
In addition, Flexxbotics said it provides smart workflows with contextualized step-by-step instructions. These instructions are based on the CNC machine and robot’s status at failure for error resolution. This way, technicians or operators know exactly what went wrong.
Ruland was also interested in the company’s open connectivity and interoperability between robots, CNC controllers, different inspection equipment, and IT and business systems. Finally, Flexxbotics said it provides extensibility to numerous workcell configurations, inspection technologies, and machinery types including Haas and Brothers CNCs, along with various dispensing machine options.
“With Flexxbotics, we have achieved our 80% utilization goal for our FANUC RoboDrill cells in less than 90 days,” Vinci said. “The optimization process that Flexxbotics provides has been invaluable
FlexxCORE the ‘backbone’ of the smart factory
Flexxbotics’ workcell digitalization technology delivers autonomous process control for machining environments utilizing robotics. The company’s flagship product, the FlexxCORE technology, connects and coordinates robots with existing automation equipment, IT systems, and people.
“We understand the complexity involved in transitioning to next-generation machining operations and the necessity for advanced robotic machine tending,” stated Tyler Bouchard, founder and CEO of Flexxbotics. “What we’re doing at Flexxbotics is enabling the world’s most sophisticated smart factory environments to embrace robot-driven manufacturing at scale.”
The company recently teamed up with Vention to release a combined machine-tending offering. The partners claimed that customers can now benefit from the combination of Flexxbotics’ system with Vention‘s MAP offering.
Customers can now use Vention’s cloud-robotic tools and modular automation hardware to design custom workcells, while also taking advantage of Flexxbotics’ software-as-a-service/hybrid system.
Credit: Source link
Comments are closed.