Listen to this article ![]() |
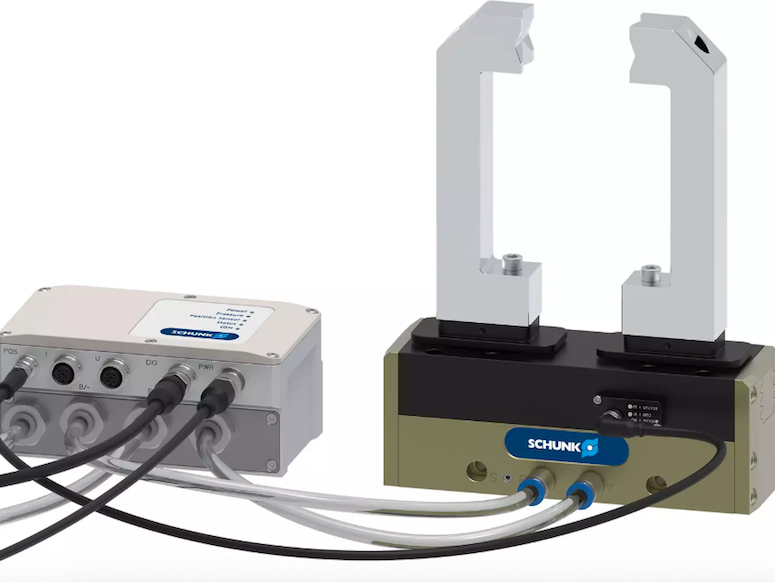
SCHUNK said its pneumatic positioning device makes pneumatic grippers more flexible through free positioning, gripping force and speed adjustment. | Credit: SCHUNK
SCHUNK released a pneumatic positioning device (PPD) that it said allows free pneumatic positioning with pneumatic grippers. SCHUNK said this solution is designed for any gripper application that requires flexibility, including robot applications that move workpieces of different sizes or in close proximity to each other.
Developed as an accessory for pneumatic grippers, the PPD is controlled via IO-Link. Together with a position sensor, any position of the gripper fingers can be approached. SCHUNK said this overcomes the gripper open/gripper closed principle. The system set-up consists of just three components: the PPD, a positioning sensor and a standard gripper.
According to SCHUNK, the setup means neither modifications nor special variants of the gripper are necessary. With the PPD, this new dimension of gripping can be retrofitted in an existing operating process.
Submit a session abstract now to be an event speaker. Submission Deadline: December 15, 2023
SCHUNK said the new PPD will enable users to optimize their cycle times as the gripper fingers don’t have to move to the end positions before and after each gripping operation. The device avoids collisions with closely positioned workpieces, as it pre-positions the gripper fingers. The gripping force can also be adjusted with the unit by adjusting the output pressure.
The unit features four integrated high-speed 2/2 valves, which together with the integrated electronics and position sensor, ensure a closed control loop. The sealed design with IP67 makes the PPD suited for use in industrial environments.
SCHUNK said the PPD can be installed at the end-of-arm, which can create a positioning accuracy of up to 0.5 mm. The PPD is available in three versions that differ in the flow rate of the internally installed valves. Size and weight always remain the same. SCHUNK said one of its own IO-Link sensors, or all common analog sensors from other suppliers, can be used as sensors for the PPD.
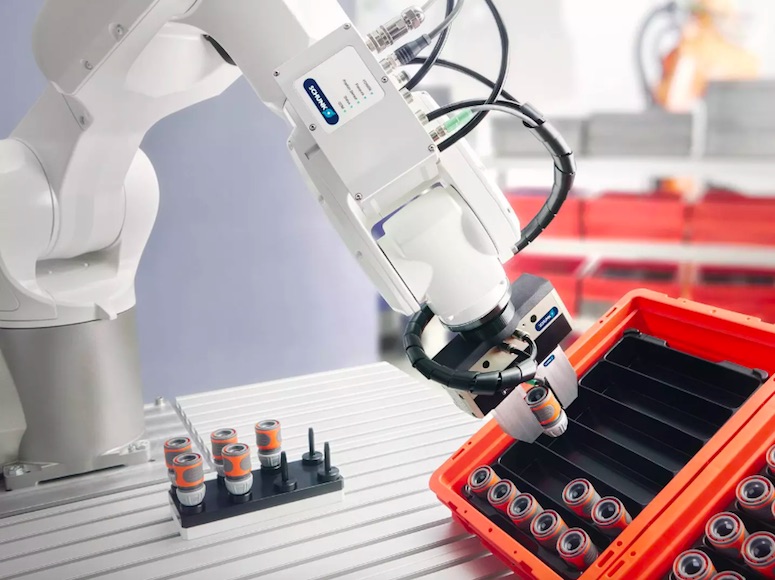
SCHUNK said collisions with closely positioned workpieces can be avoided since the gripper fingers are pre-positioned with the pneumatic positioning device. | Credit: SCHUNK
Credit: Source link
Comments are closed.