Listen to this article ![]() |
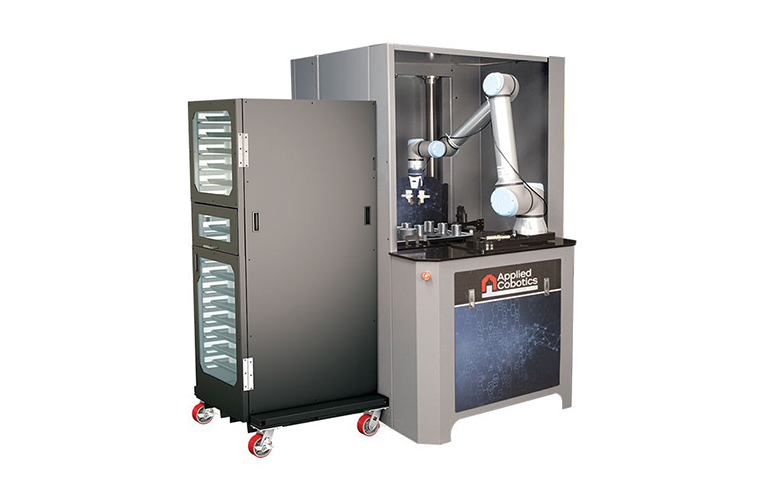
PBC Linear and Universal Robots’ Applied Cobotics Cobot Feeder. | Source: Universal Robots
PBC Linear (Pacific Bearing Company), a producer in linear motion systems, has announced that its Applied Cobotics Cobot Feeder, a CNC machine feeding application kit that delivers and stages parts to be placed into a machining process, has received Universal Robots+ (UR+) partner certification from Universal Robots (UR).
PBC Linear’s Applied Cobotics Cobot Feeder includes a base storage and retrieval unit with a UR cobot pedestal, an enclosed steel rack dunnage tower with a 17-tray capacity that safely stores up to 50 pounds of material, an HMI touch screen display for easy lift control, Ethernet IP, Modbus, and standard UR cobot communications.
Designed to address material handling and labor shortage issues, the Cobot Feeder boosts UR cobot production without significant increases in labor. PBC Linear’s Cobot Feeder helps manufacturers achieve a higher return on their investment (ROI), with paybacks in as little as two months with the Cobot Feeder and UR cobot operating 24/7. By reliably loading and unloading dunnage trays that a UR cobot can consistently access, this versatile CNC machine-tending tool provides a standardized platform for storing, staging, and delivering parts into a position that the UR cobot can reach for loading and unloading.
“Machine tending is a critical process in manufacturing and one of the most popular applications for UR cobots,” Joe Campbell, senior manager of applications development at Universal Robots, said. “By constantly feeding the cobot new parts to accurately pick and place, Applied Cobotics optimizes this process significantly. We’re excited to include the Cobot Feeder in the UR+ product portfolio, benefitting our rapidly growing customer base looking to automate this task.”
The UR+ platform is a comprehensive ecosystem of certified partner products designed to seamlessly integrate with UR cobots. Operating a Cobot Feeder alongside a UR cobot provides several benefits to shop floors:
- Higher efficiency: It reduces changeovers and robot downtime, leading to increased cobot output.
- Increased productivity: It provides a significant boost in cobot production, up to 16 times more than single-tray applications.
- Cost containment: The Cobot Feeder helps mitigate the impact of rising labor costs. One operator can oversee multiple stations, allowing them to focus on production flow and quality control.
- Greater flexibility: The Cobot Feeder enables shop floors to adapt to dynamic markets with multiple parts runs, lights-out automation, and shorter lead times.
- Recruitment and retention: The Cobot Feeder helps create a more engaging, more fulfilling, and safer work environment, making the workplace more appealing to young recruits and helping to retain experienced workers who seek skill development and an improved workplace atmosphere.
- Higher return on investment: Recovering the cost of the Cobot Feeder, the UR cobot, and accessories occurs in approximately six months running a single eight-hour shift or in as little as two months when operating 24/7. To learn more, access the online ROI Calculator today.
Using sample parts or CAD files, the PBC Linear Applied Cobotics team can provide flexible, cost-effective, custom-molded, or machined nests in as little as a day, allowing manufacturers to tailor dunnage trays to meet specific application requirements and quickly accommodate new product introductions.
Credit: Source link
Comments are closed.